6” Class 300 AOGV
The Izomax patented AOGV is a mechanical isolation tool which can be temporarily assembled on any pair of flanges in a pressurised process system. The tool is used to replace gaskets, install, and retrieve blind spades to facilitate intrusive maintenance. The blind spade or a combination of several spades in different locations can replace the function of valves and provide positive isolation for vessels, valves, or parts of a process plant. Bleeding or purging through the blind spade can also be facilitated. The AOGV design meets the requirements as per EU Pressure Equipment Directive (PED) (2014/68/ EU) and EN 13445 – Unfired Pressure Vessels. Upgrade your maintenance process with the reliable and innovative AOGV.
Dimensions
2340 mm x 510 mm x 430 mm [92 in x 20 in x 17 in]
Weight*
570 kg / 1260 lbs
Flange Class
ASME B16.5 class 300
Design Code
PED 2014/68/EU/ – EN 13445
Design Pressure
50 bar / 725 psi
Design Temperature
-29 °C to +50°C / -20°F to +122°F
Body Material
Pressure vessel steel (P355/P460)
Gasket
SPW ASME B16.20 or Sheet Gaskets
* The weight of the AOGV is suspended at all times by chain hoists attached to the superstructure or scaffolding above the actual flange.
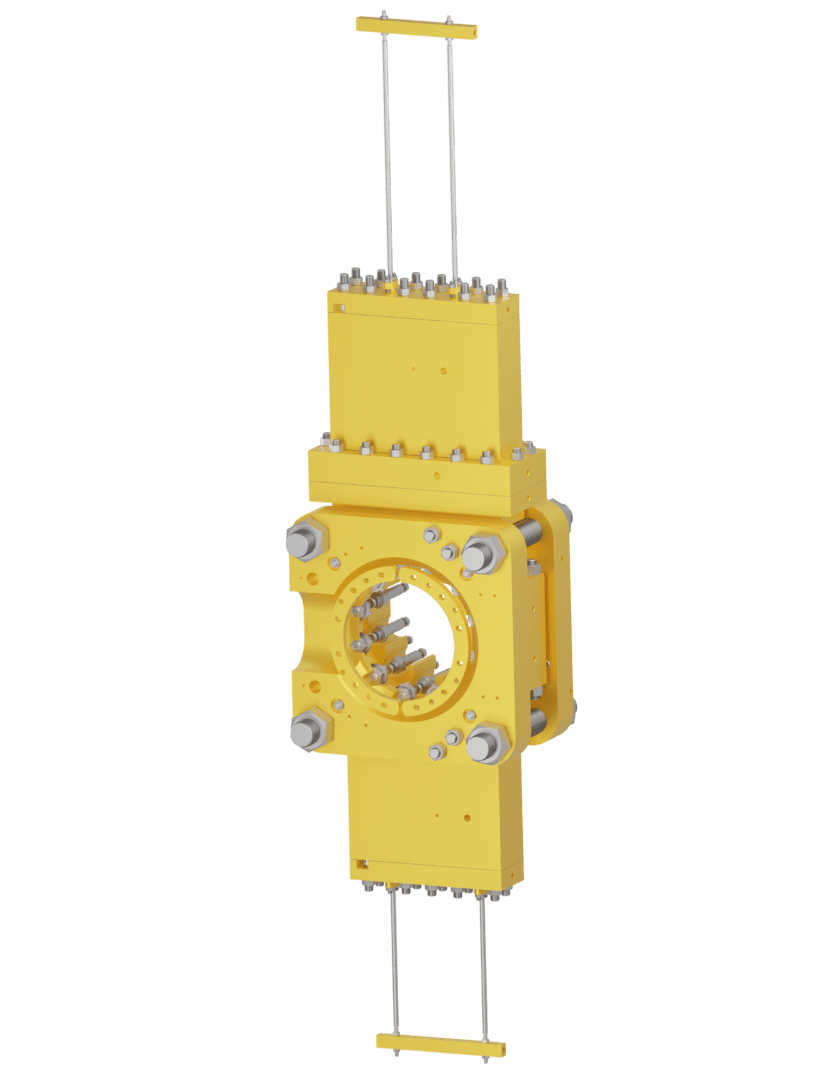
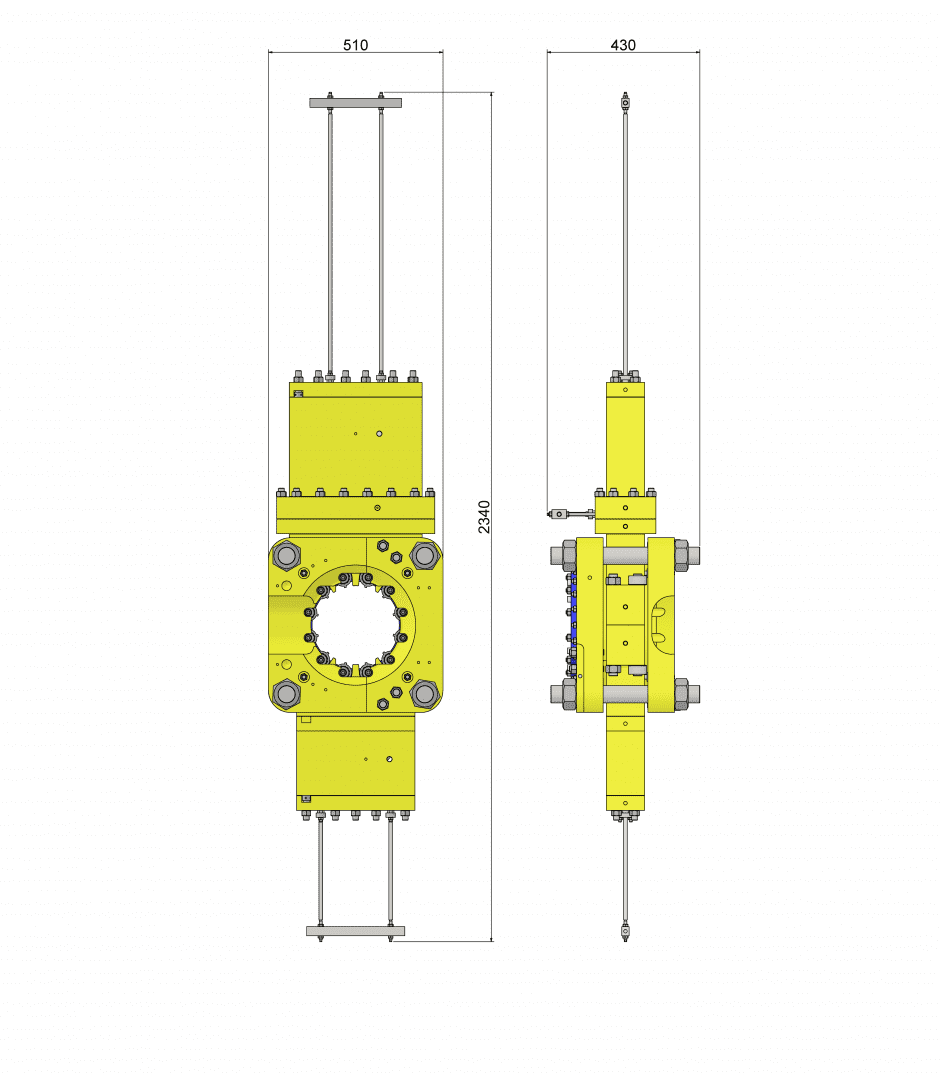
The AOGV safely manipulates the flanges, positions a blind spade between the flanges, removes the old gasket or valve, and inserts a new one. Flange bolts are accessed and torqued with ordinary bolting equipment. Plant reinstatement is a critical element of an isolation activity. The AOGV is a temporary tool that can be installed anytime during normal plant operation and allows important maintenance and inspection work to be performed with less impact on the process plant. The AOGV aims to perform interventions with significantly less impact on production than traditional methods. The process fluid largely remains in the operating system, which reduces environmental impact, cost, and downtime.
Contact
T: +47 51 44 32 00
E: post@izomax.com
Contact us
Our friendly team would love to hear from you.