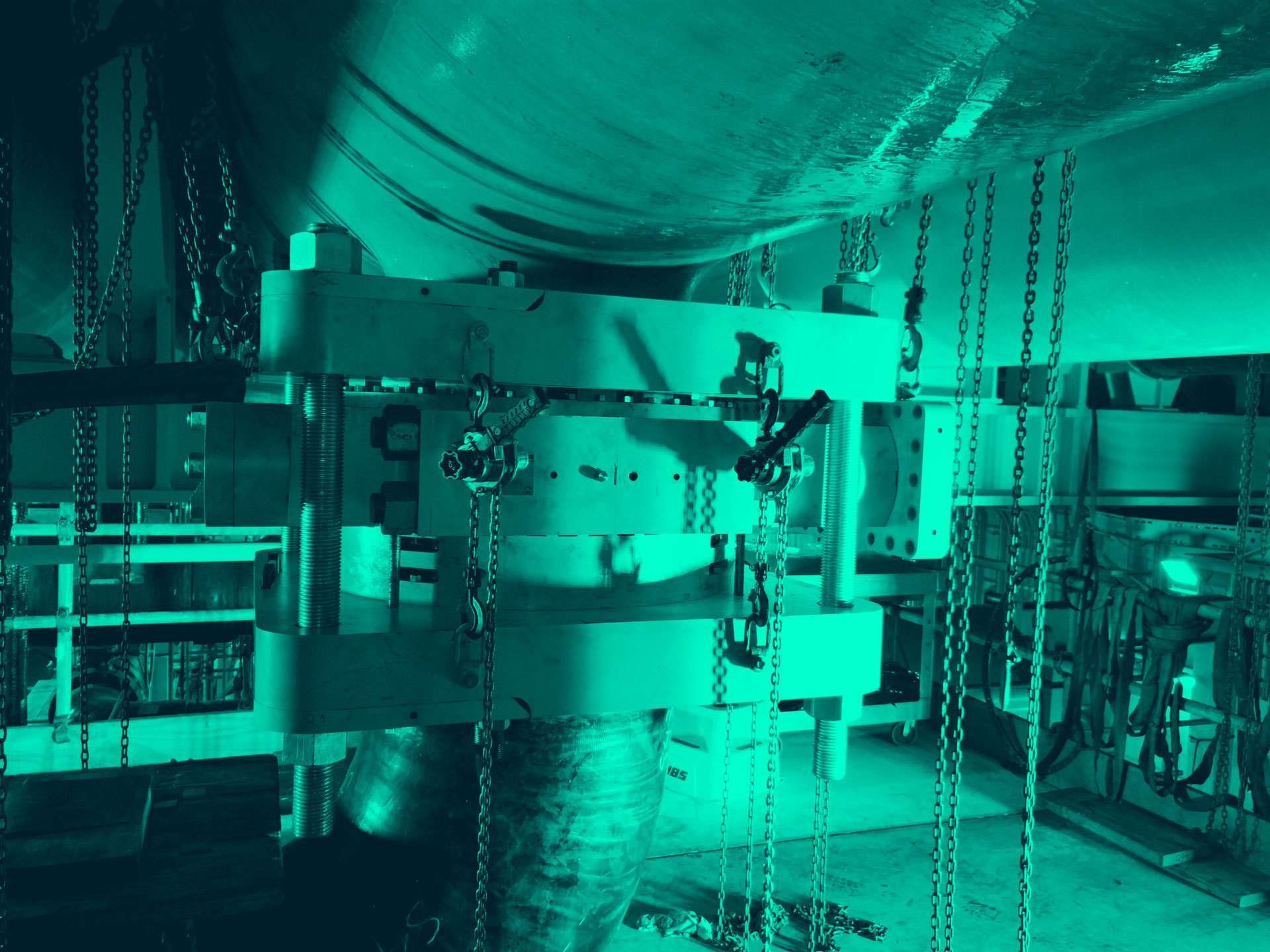
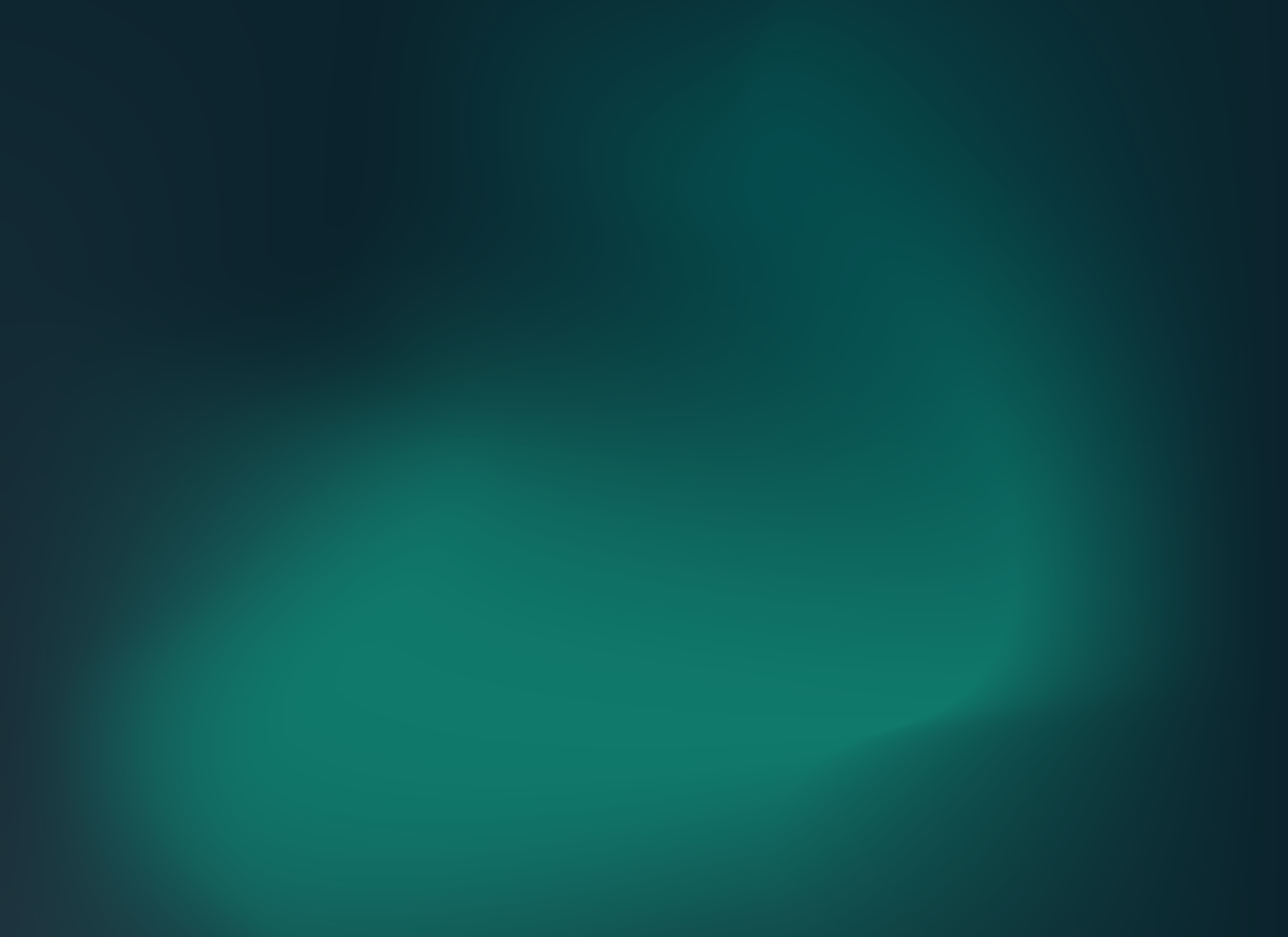
Case Study
Production shutdown avoided during offshore fire safety system maintenance
A major oil and gas platform, producing close to 100,000 BOE daily, reported leaks in the cooling systems of all four diesel-powered firewater pumps. Without isolation valves in place, the isolation of each pump for this critical maintenance would have resulted in a production shutdown. Through deployment of the Izomax AOGV mechanical isolation system, a shutdown was avoided, resulting in savings of approximately $80m USD.
Challenges
The platform was equipped with a total of four firewater pumps, constantly on standby in case of fire, and ready to be deployed within seconds. As all were reported to be leaking, the lack of a 100% fire system redundancy created significant safety issues on the platform. Each pump’s cooling system consisted of a heat exchanger between the internal cooling liquid and sea water. The outlet of the sea water system cooling the heat exchanger required back pressure to avoid damaging to the pumps during start-up, achieved by connecting each pump to a common manifold and a 6 meter (19,6 ft), 16 inch vertical upward pipe before the outlet. Valves were not present on any of the pump outlet spools, so the leakages could not be addressed without a full production shutdown. Other types of isolations such as plugging or freezing methods were evaluated by the customer and deemed unsuitable.
Solutions
The Izomax patented AOGV is a mechanical isolation tool which can set and retract a blind spade in a pair of flanges on a pressurised process system. The blind spade or a combination of several spades in different locations can facilitate the replacement of valves and pumps. The AOGV can also be used to take a vessel out of a closed loop temporarily for safe entry and bringing it back on-line, whilst the main process is kept in continuous operation. The AOGV system had been previously deployed on this platform. Aware of its capabilities and benefits, the platform crew planned the operation with a specific AOGV tool in mind.
Testing, planning, preparation
Izomax conducted an on-site survey, providing our specialist engineers with the data to ensure a perfect fit between the AOGV and flanges, with the flexibility for adjustment if required.
Flange obstacles also required that the Izomax team design and manufacture a bespoke gasket receiver housing. On each pump a 2 inch class 150 inlet and 4 inch class 150 outlet required isolation. To facilitate cost efficient future maintenance, new spools with valves were mounted between the motor and the common manifold. All required equipment was prefabricated – ready to be mounted and installed as soon as the AOGV isolations were set.
Site Operation
Following a Safe Job Analysis and work permit issue, the AOGV blind spades were set on the downstream side on both the 2 inch inlet and 4 inch outlets, between the common manifold and the heat exchanger. The threaded blind spades were bolted to the flanges towards the manifold. After setting the spades, the AOGVs were removed, the cooling water inlet line on the motor was closed and the system drained. As soon as the system was drained, new spools with valves were inserted, the AOGV re-assembled, and the blind spades removed. This process was repeated for all four pumps, resulting in a total of eight AOGV isolations.
Outcome
The Izomax engineering and support team worked closely with the customer to plan for flawless execution. The entire operation including site survey, manufacture, testing and offshore work was performed without HSSE incidents or non-productive time. Due to the safety critical systems involved, planning, scheduling and rapid deployment was essential – resulting in Izomax successfully completing all work ahead of plan.
As with the vast majority of Izomax AOGV mechanical isolation work, no hot work was required, saving the operator considerable time and costs related to planning and executing hot work, in addition to mitigating complex HSSE risk. System integrity was maintained throughout the operation, with plant returned to original status and condition.
The Izomax team enabled an estimated cost saving of $80m USD as a direct result of not shutting down production. Other technologies were evaluated by the customer but deemed unsuitable, hence this direct saving could not have been achieved without using Izomax AOGV technologies.