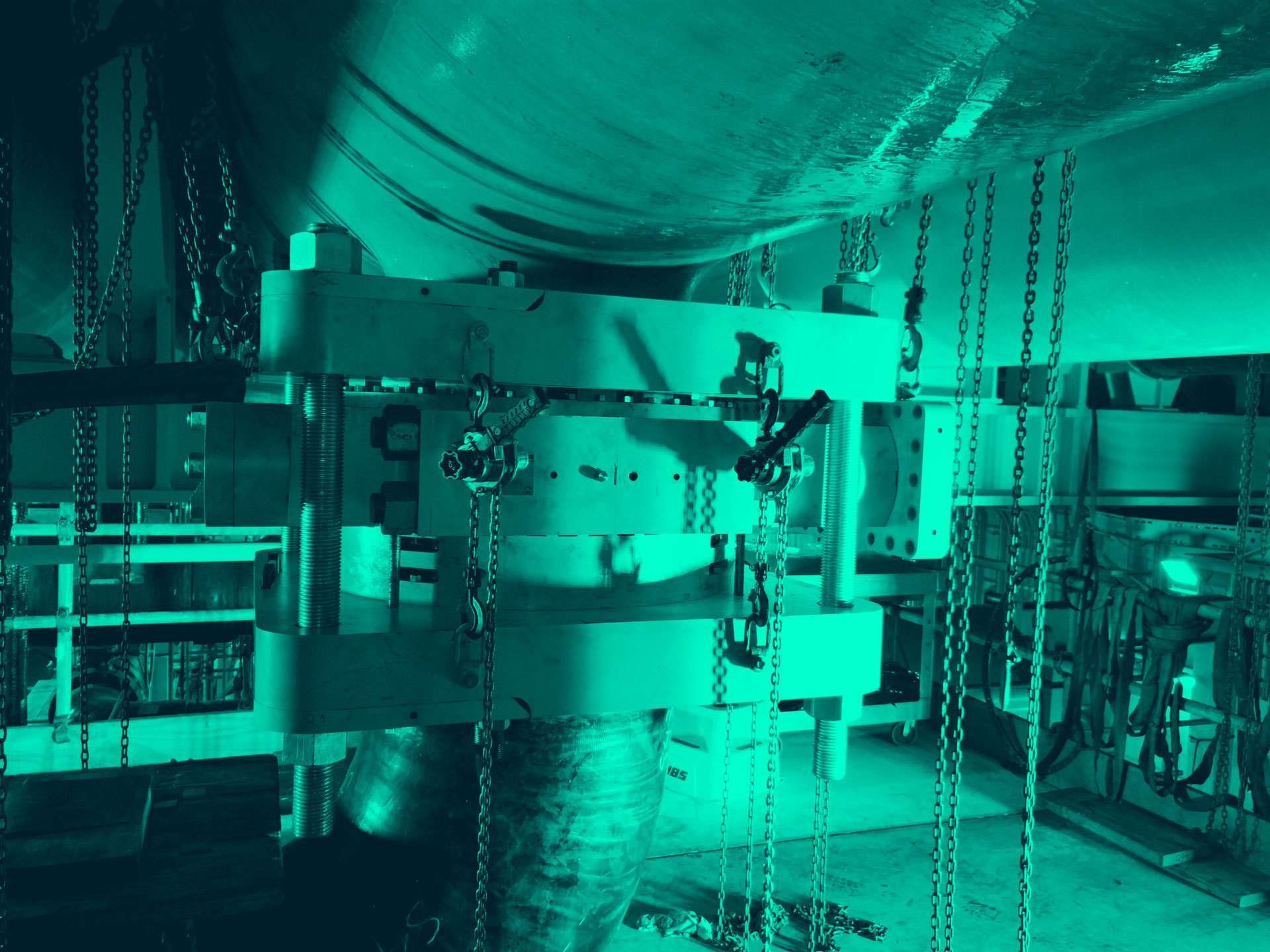
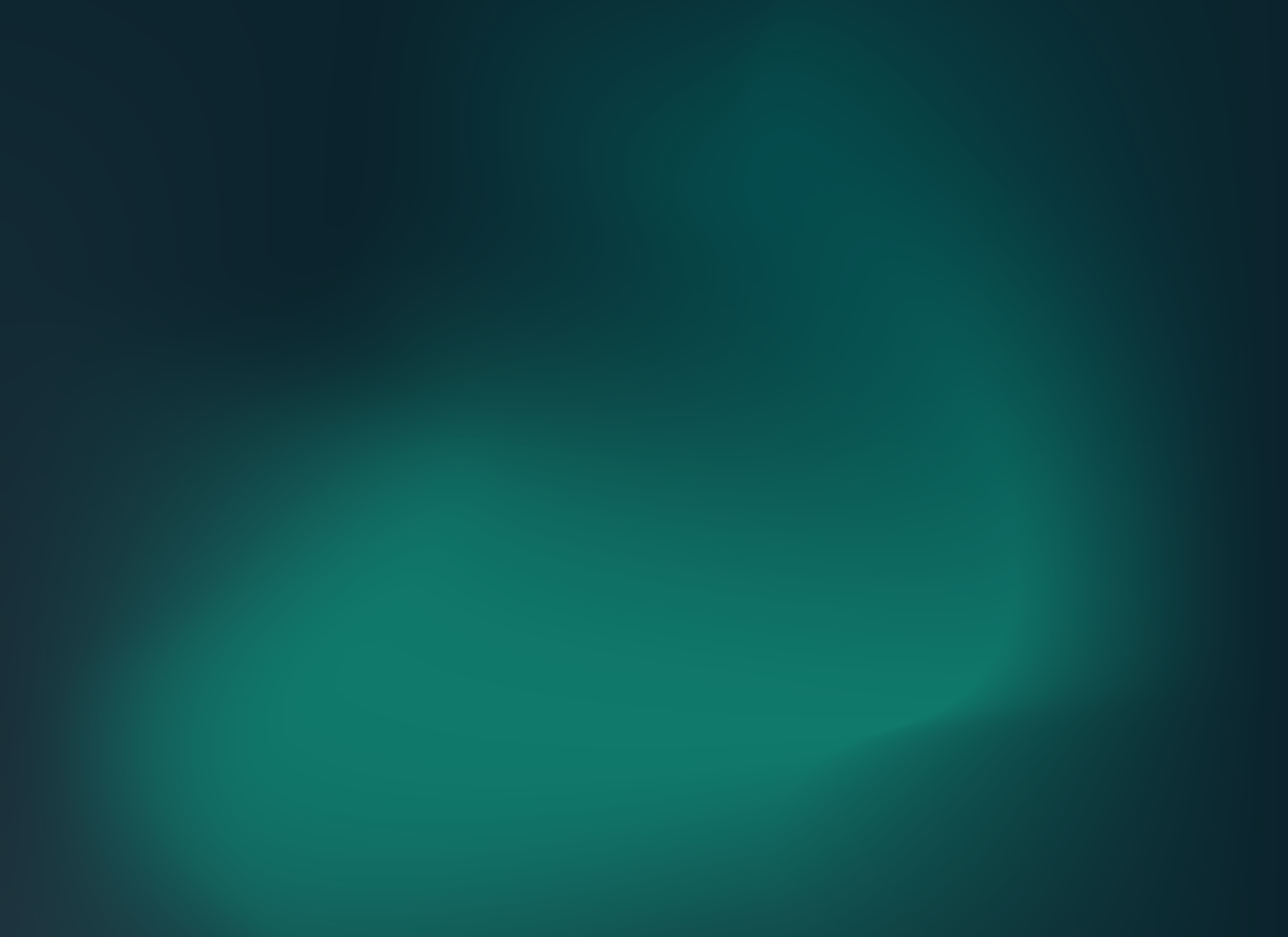
Case Study
Offshore installation shutdown avoided using Izomax AOGV
At a semi-submersible oil and gas production facility, a passing 4 inch class 150 valve required urgent isolation to prevent Hydrocarbon gas from entering the flare system. From initial enquiry, Izomax designed, engineered, and enabled replacement of the valve in just four weeks, with no loss of productive time.
With gas prices heading towards record highs, the operator was looking for a solution which would allow production to continue, avoiding the major costs, risks and complex operations associated with shutdown and draining of the process inventory.
Challenges
Semi-submersible production facilities in harsh environments operate in a heavily regulated segment of the oil and gas industry. Every decision taken around modification or intervention must be thoroughly reviewed from a safety critical perspective. The North Sea is a high-cost environment where robust, timely and efficient solutions are essential. Hot work carries additional risks, cost and complexity offshore, and can be avoided using Izomax mechanical isolation systems. In this instance, the passing valve between the process plant and the high pressure flare system needed urgent maintenance. There were no suitable means for isolation near the maintenance point, so intervention with alternative technology was a must to minimize or negate production delays. During the site survey, the Izomax team identified the requirement for a specially designed lower integrity clamp to fit between the valve housing and pipe spool flange. The ultimate challenge was to avoid a full production shutdown which would be necessary using conventional intervention technologies.
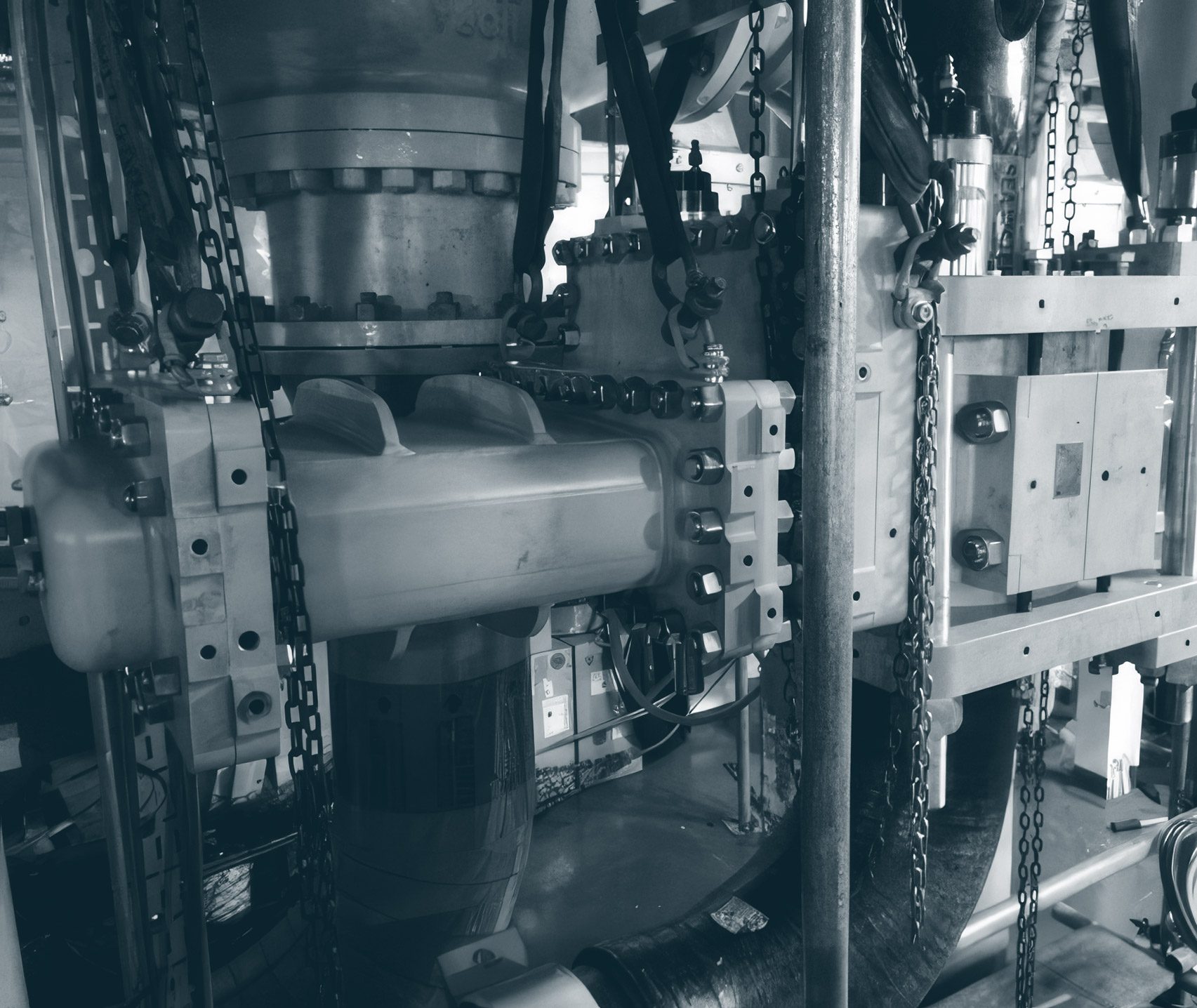
Solutions
The Izomax patented AOGV is a mechanical isolation tool which can set and retract a blind spade in a pair of flanges on a pressurised process system. The blind spade or a combination of several spades in different locations can facilitate the replacement of valves and pumps. The AOGV can also be used to take a vessel out of a closed loop temporarily for safe entry and bringing it back online, whilst the main process is kept in continuous operation. Providing positive isolation, the AOGV was identified as the solution, facilitating intrusive maintenance on a live flare system with a spade set in between the valve and pipe spool leading to the flare. The semisubmersible remained in normal operation whilst the pressurised HC line was split and the valve replaced.
Testing, planning and preparation
One 4 inch ASME Class 150 AOGV mechanical isolation tool was commissioned for the work scope. Prior to manufacturing and full-scale workshop testing, Izomax planned offshore site activities, including a site survey, in collaboration with the operator.
During the sire survey It became apparent that the lower integrity clamp had to be specially manufactured to fit between the valve housing and pipe spool flange. By utilising complex area-specific 3D scans, the Izomax team engineered and manufactured the integrity clamp to fit the valve flange. The AOGV was proof tested at 1.43 times the design pressure to ensure no leakages in the event of pressure build up due to flaring. Izomax field engineers gave multiple presentations to the operator’s offshore employees, ensuring their understanding of the technology and associated procedure prior to executing the work.
Site operation
The Izomax crew was mobilised and performed a faultless operation during which a spade was set – isolating the passing valve and enabling valve replacement. The isolation spade was set without causing non-productive time or any health, safety and environmental issues and ultimately saved the operator the cost of a significant facility shutdown.
Outcome
The Izomax engineering and support team ensured a rapid response, with an enquiry to execution and job complete cycle of just four weeks. The entire operation including site survey, manufacture, testing and offshore work was flawless with no HSE incidents or non-productive time.
As with all Izomax AOGV mechanical isolation work, no hot work was required, saving the operator considerable time and costs related to planning and executing hot work, in addition to mitigating complex HSSE risk. System integrity was maintained throughout the operation, with plant returned to original status and condition.
The Izomax team enabled an estimated cost saving of $15m USD as a direct result of not shutting down production. This direct saving would not have been achieved without using Izomax AOGV technologies.