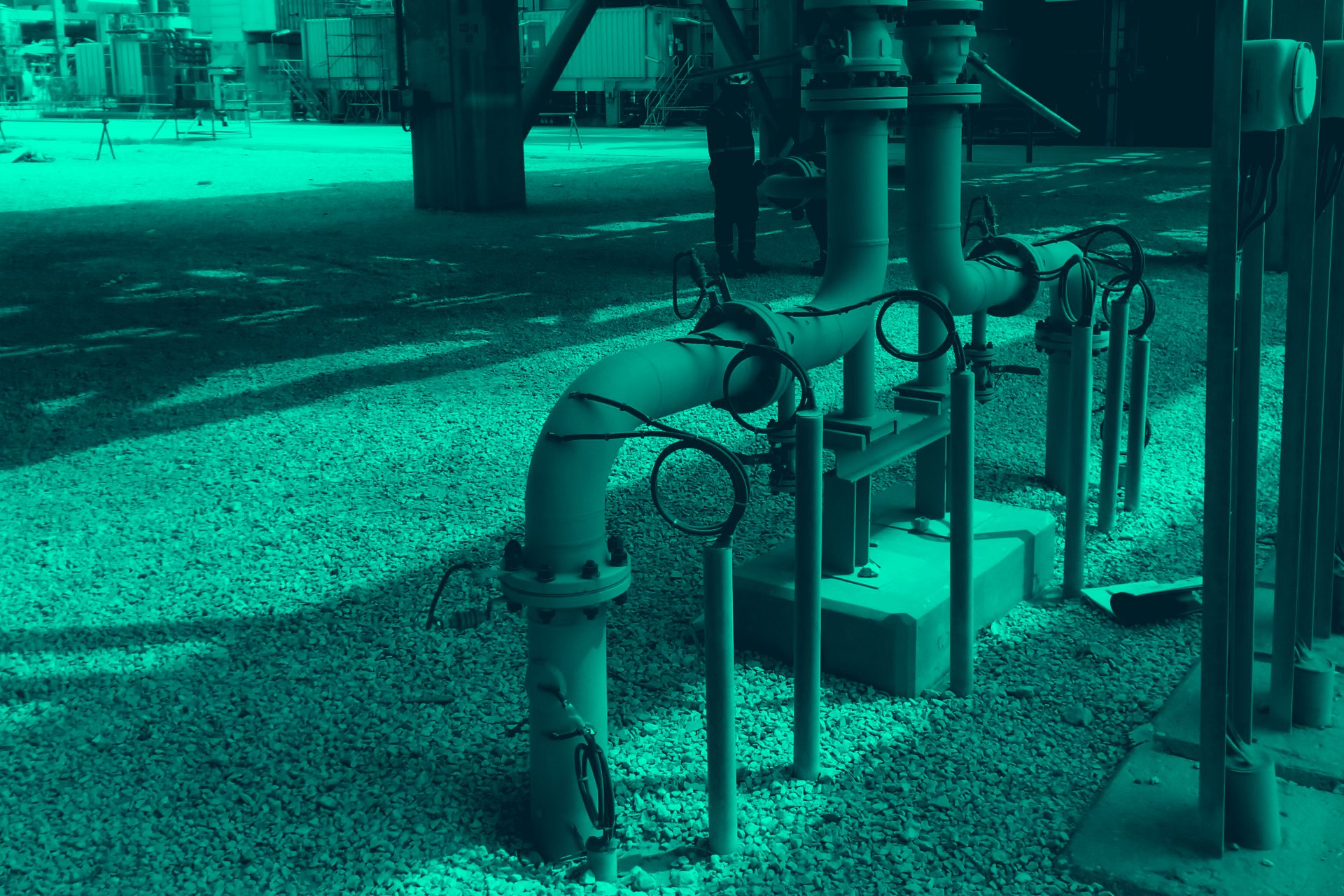
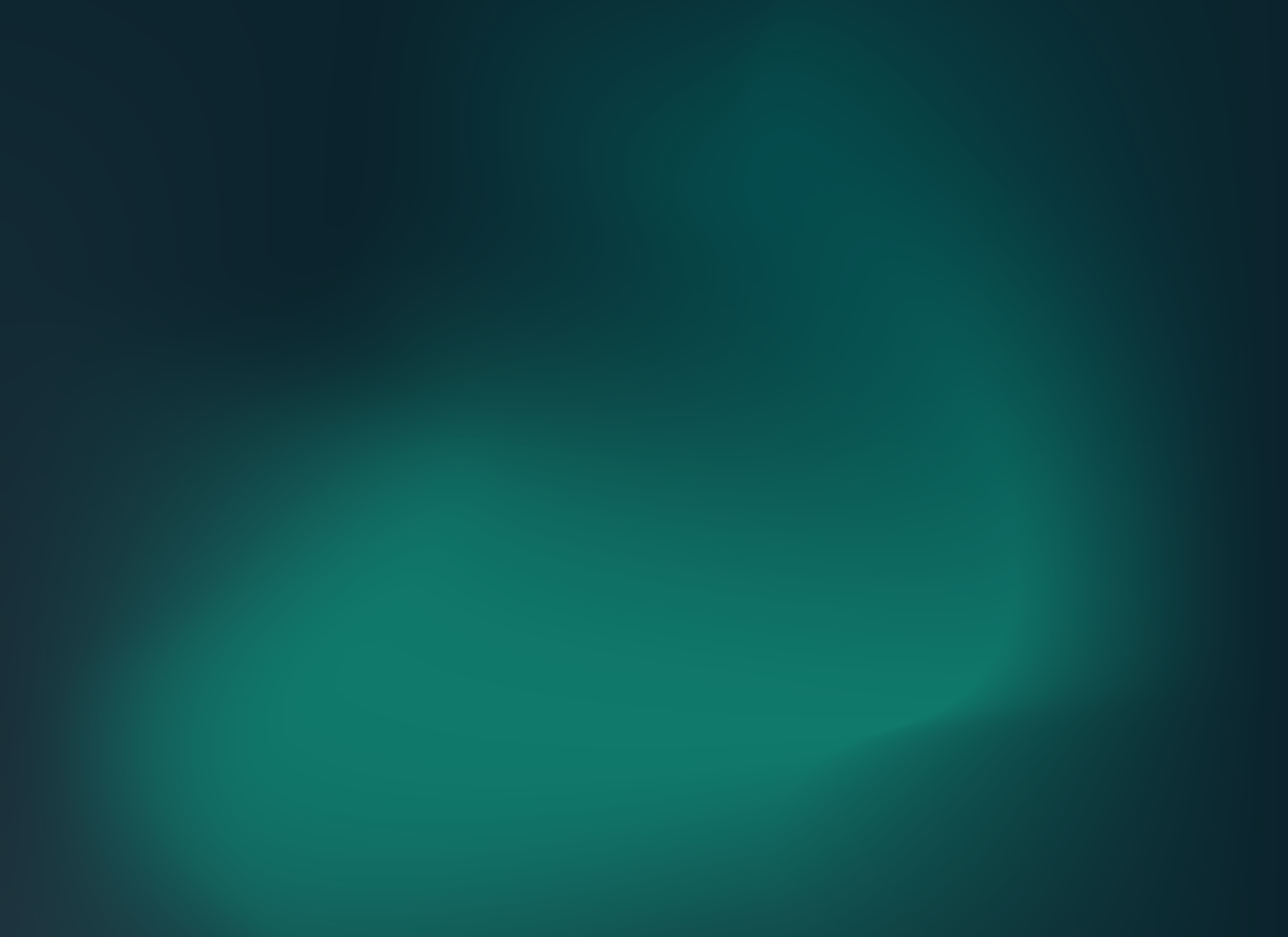
Case Study
Izomax performs Isolation and replacement of 3 critical valves at Qatar GTL plant
A Supermajor in Qatar required a solution to address problems with three passing valves, which were safety critical components in a flare line cooling water distribution train.
The customer had not used the Izomax AOGV mechanical isolation system in the country before but had received recommendations from their global organization regarding the system performance and efficiency. Considering no previous local experience, the GTL site team decided to utilize the AOGV to isolate one side of each valve,
whilst using traditional hot tap techniques to isolate the other side of the valve. This approach would allow the customer to evaluate and benchmark the AOGV performance and efficiency directly with traditional technologies.
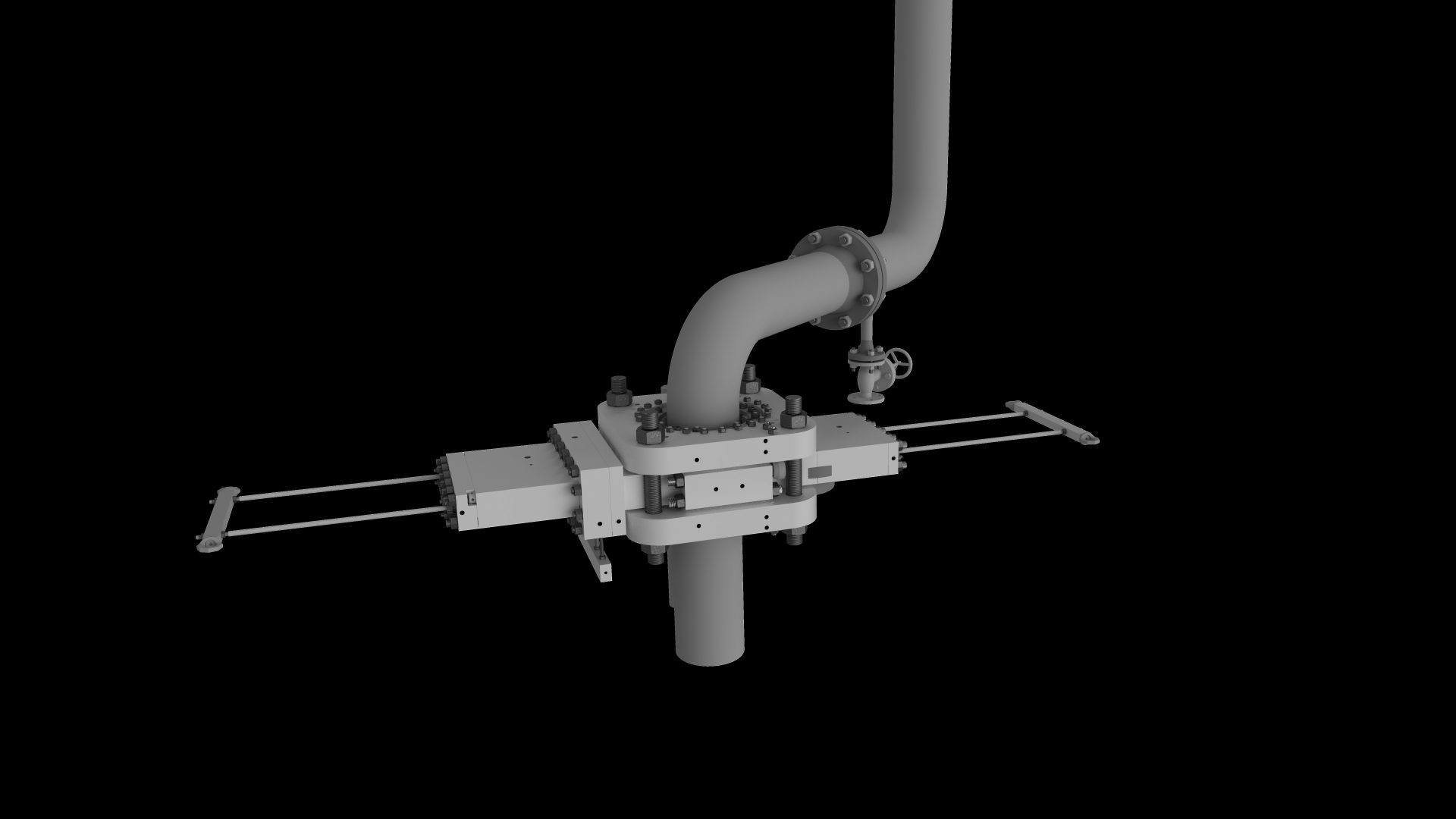
Challenges
Three passing valves (which were inoperable and stuck in a partly open position) required urgent maintenance.
The operator was unable to verify the exact position of each valve, but estimated they were more than 80% closed. This meant that the lines were
under pressure and flow was occurring at each location.
The hot tap process planned at one side of each faulty valve could not take place until flow was stopped, hence the AOGV had to isolate the line prior to the hot tapping operation.
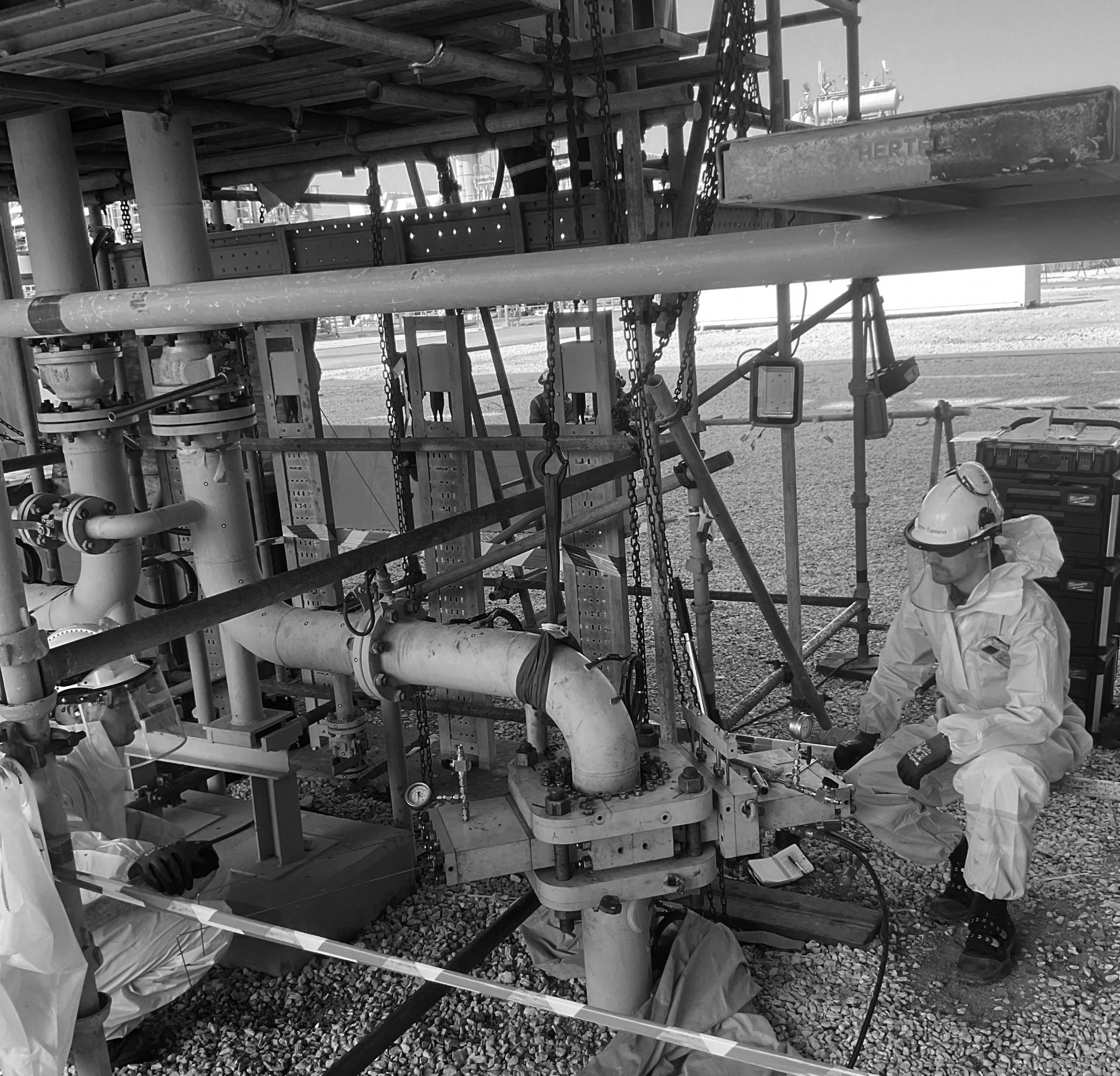
The AOGV mechanical isolation system has limitations operating under flow. The flow was unknown (due to the unknown valve positions), making the operation a real challenge.
Piping rigidity at suggested isolation points was challenging, meaning that careful analysis was required to ensure that the flange pair could be safely separated during isolation.
The plant would need to be shut down if the AOGV isolation was not successful to allow intervention by hot tapping.
Solutions
The customer concluded an in-depth evaluation of the propriety Izomax AOGV mechanical isolation system.
The Izomax team performed a site survey in conjunction with the customer which included 3D scanning to ensure accessibility and exact system dimensions.
Due to pipe rigidity at the customer selected isolation points, the Izomax survey engineer recommended alternative isolation points which would allow flange pair separation and isolation spade insertion, without unduly stressing the piping system. Izomax assisted with independent pipe stress analysis and modelling to ensure the optimum isolation points had been chosen.
An off the shelf, 6” 150 class AOGV tool was utilized for all three isolations. Flow scenarios were estimated to confirm the AOGV would function at the flow rates for valves in the estimated 85% closed position.
Schedules and plans were detailed, ensuring that the Izomax team, Hot Tapping contractor and customer site personnel would be able to execute flawlessly, without unplanned interruptions or scheduling constraints.
SJA (safe job analysis) was performed, in addition to pre-job and toolbox meetings. All relevant personnel were fully informed of the entire process to ensure that safety and operational efficiency were fully understood with all relevant parties aligned.
Outcome
Efficient completion of this project was critical. With three damaged valves in flare line the cooling system, safety and plant efficiency could only be assured by a shutdown in the event the AOGV isolations were not successful.
The isolation points suggested by Izomax during the site survey were selected and used without operational issues.
Composite gaskets at each flange pair isolation point were replaced as an integral part of the AOGV mechanical isolation system process.
All three isolations were performed safely, with each of the valves replaced in planned sequence. Scheduled to take place over a 3 week period, the entire operation was completed 1 full week ahead of schedule.
Izomax operations were all accomplished without NPT (non-productive time), or HSE incidents.
The customer was able to benchmark the Izomax AOGV mechanical isolation system against traditional hot tapping processes. Whilst the detailed conclusions have not been shared with Izomax, the customer has given overall feedback with a high degree of satisfaction and is already engaging Izomax in several projects at the
same site.
As with the vast majority of Izomax AOGV mechanical isolation work, no hot work was required, saving the operator considerable time and costs related to planning and executing hot work, in addition to mitigating complex HSSE risk. Plant and system integrity was maintained throughout the operation, with plant returned to original status and condition.
Identifying suitable existing AOGV systems led to lower costs whilst minimizing the carbon footprint of the entire intervention.