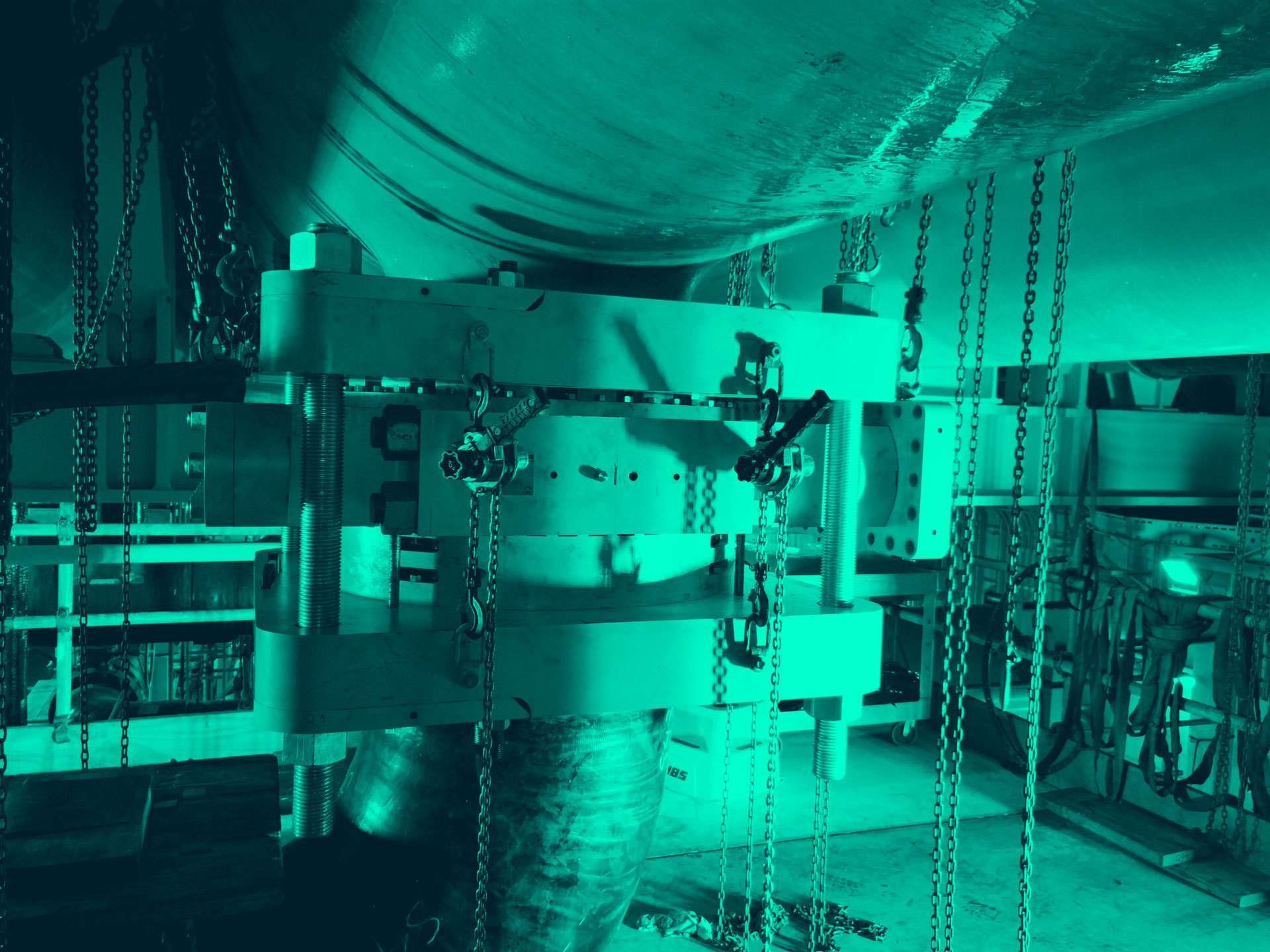
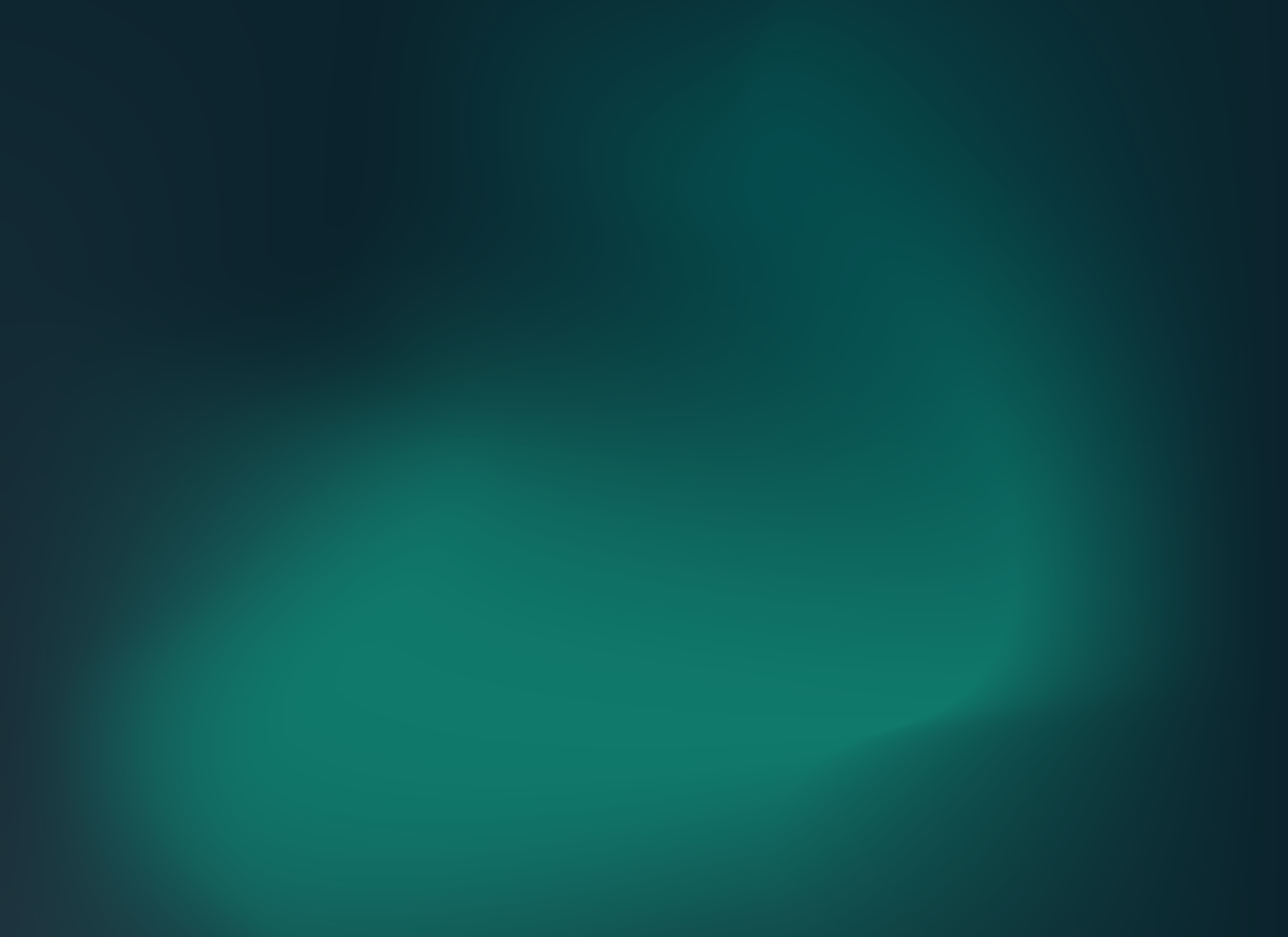
Case Study
AOGV solves long-term stuck valve issue on major LNG plant
A 36 inch butterfly valve on the flare line of a major onshore LNG plant had been stuck in the closed position for several years, preventing use of the backup flare system.
A partial facility shutdown was planned as part of the normal facility maintenance routines and use of the backup flare system was critical to avoid a full shutdown. Conventional intervention methods were estimated to have an incremental shutdown of one month. Replacing the failed butterfly valve prior to maintenance was the key enabler to allow operational continuity, mitigating an extended shutdown.
The facility is one of the world’s largest suppliers of LNG. Current global energy demand and supply issues meant a halt in production would have major impacts on the plant operator and customers alike.
Challenges
A butterfly valve on a 36 inch class 150 flare line operating at 1.5 bar (22 psi) pressure had been stuck in a closed position for an extended period. The stuck valve prevented the backup flare system from being used, thus limiting the options available to undergo planned maintenance without shutting down. The working temperature of the line could range from ambient to cryogenic in the event of a sudden relief of liquids, and the faulty valve needed to be replaced. Solutions were required to mitigate HSSE risk associated with the valve replacement, as there were no suitable built-in isolation points close to the stuck valve. The plant operator had evaluated alternatives, concluding that few, if any, robust or cost-effective solutions were available.
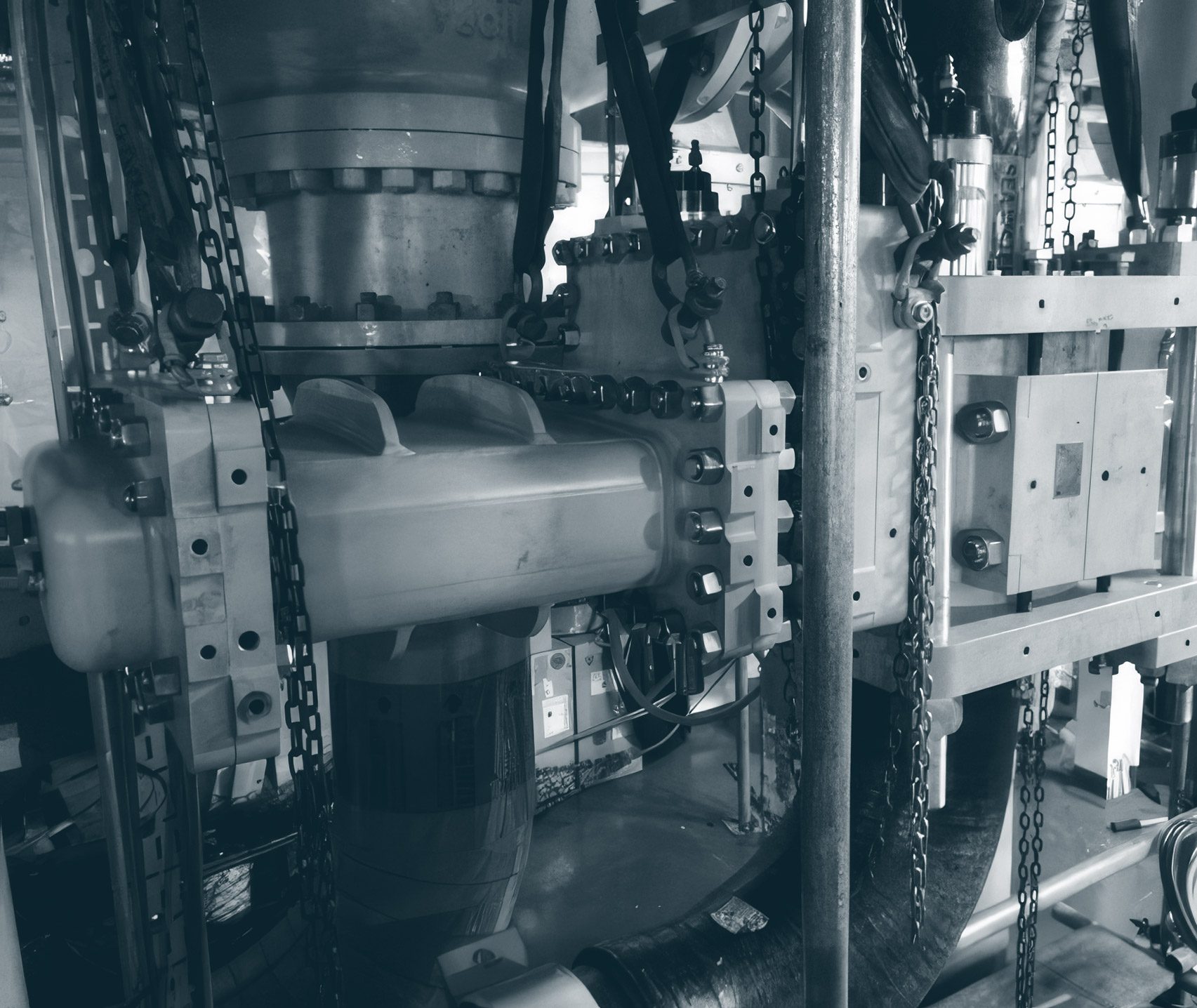
Solutions
The Izomax AOGV is a patented mechanical isolation tool which can set and retract a blind spade in a pair of flanges on a pressurised process system without hot-work. The blind spade or a combination of several spades in different locations can facilitate the replacement of valves and pumps. The AOGV can also be used to take a vessel out of a closed loop temporarily for safe entry and bringing it back on-line, whilst the main process is kept in continuous operation.
Testing, planning & preparation
A 36 inch ASME class 150 AOGV mechanical isolation system – the largest developed to date – was designed, engineered, and manufactured for the application. The design incorporated geometrical constraints from the site and was performed according to the requirements of the Pressure Equipment Directive (PED), following the unfired pressure vessel standard EN 13445. The AOGV design was verified by FEM/FEA (Finite Element Analysis) which was performed by a third party. The AOGV’s conformity was assessed by DNV, including a review of the design calculation report, evaluation of material selection, as well as follow-up of production, welding, material traceability, and proof testing.
The pipe flexibility was analysed according to the requirements of the pipe system standard; the stress levels due to pipe displacement were found to be within the limits of the piping design code.
Working closely with the facility owner, detailed planning both for site preparations and operations was performed. A HAZID was conducted, and the customer attended a Factory Acceptance Test at the Izomax facility in Stavanger.
Testing of the AOGV mechanical isolation system was performed with liquid nitrogen at -196 °C (-320 °F). The site operation was rehearsed in a mock-up rig prior to shipment to the site by same Izomax crew due to perform the operation on site. The operational procedure described the main steps of the entire site operation including elements of safe handling, installation, and operation of the AOGV mechanical isolation tool.
Site operation
Scaffolding and rigging support were supplied by the site owner for the operation. As multiple personnel would be working simultaneously in a relatively confined space, the coordination of activities had to be well planned, with communication a key element to the wider facility team. The Izomax AOGV mechanical isolation system was installed and operated by a team of three trained Izomax technical specialists, based on the established site procedures. The Izomax AOGV mechanical isolation tool was suspended throughout the operation, so the pipework did not carry any additional loads. Following installation and leak testing, the flanges were separated toward the bend side of the line as planned via the rigging arrangement. Required separation of the flanges was approximately 30mm (1 ³/₁₆ inch). After achieving separation, a blind spade was inserted and bolted up to the upstream flange to provide a positive isolation for the execution of the work. Following the AOGV mechanical isolation procedures agreed with the Facility team during the FAT, the faulty valve was safely removed, and a new valve installed by the site owner’s personnel. The AOGV mechanical isolation system was reinitiated, the blind spade removed, and the system brought back to normal operation. The main flare was operational throughout the entire operation.
Outcome
The entire operation was completed without any HSSE incidents or downtime and to the client’s full satisfaction. The AOGV mechanical isolation system enabled rectification of a long-term problem to which the site owner could not provide a solution that had an acceptable risk level; alternative technologies were evaluated but the operator deemed them to pose unacceptable risks. The Izomax AOGV cryogenic mechanical isolation tool was engineered, manufactured and delivered on-schedule, despite the fact that it was the largest tool designed and manufactured at that point in time. In addition, the work site was on the African continent, posing additional logistics challenges which were all handled professionally from mobilisation end to end.
As with the vast majority of Izomax AOGV mechanical isolation work, no hot work was required, saving the operator considerable time and costs related to planning and executing hot work, in addition to mitigating complex HSSE risk. System integrity was maintained throughout the operation, with plant returned to original status and condition.