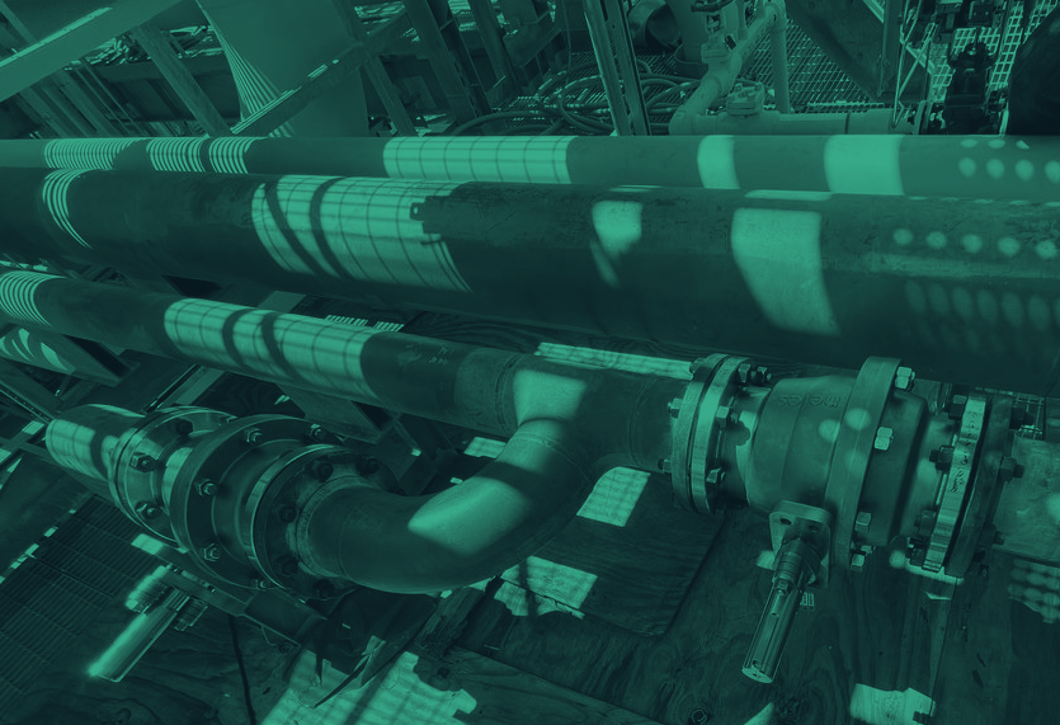
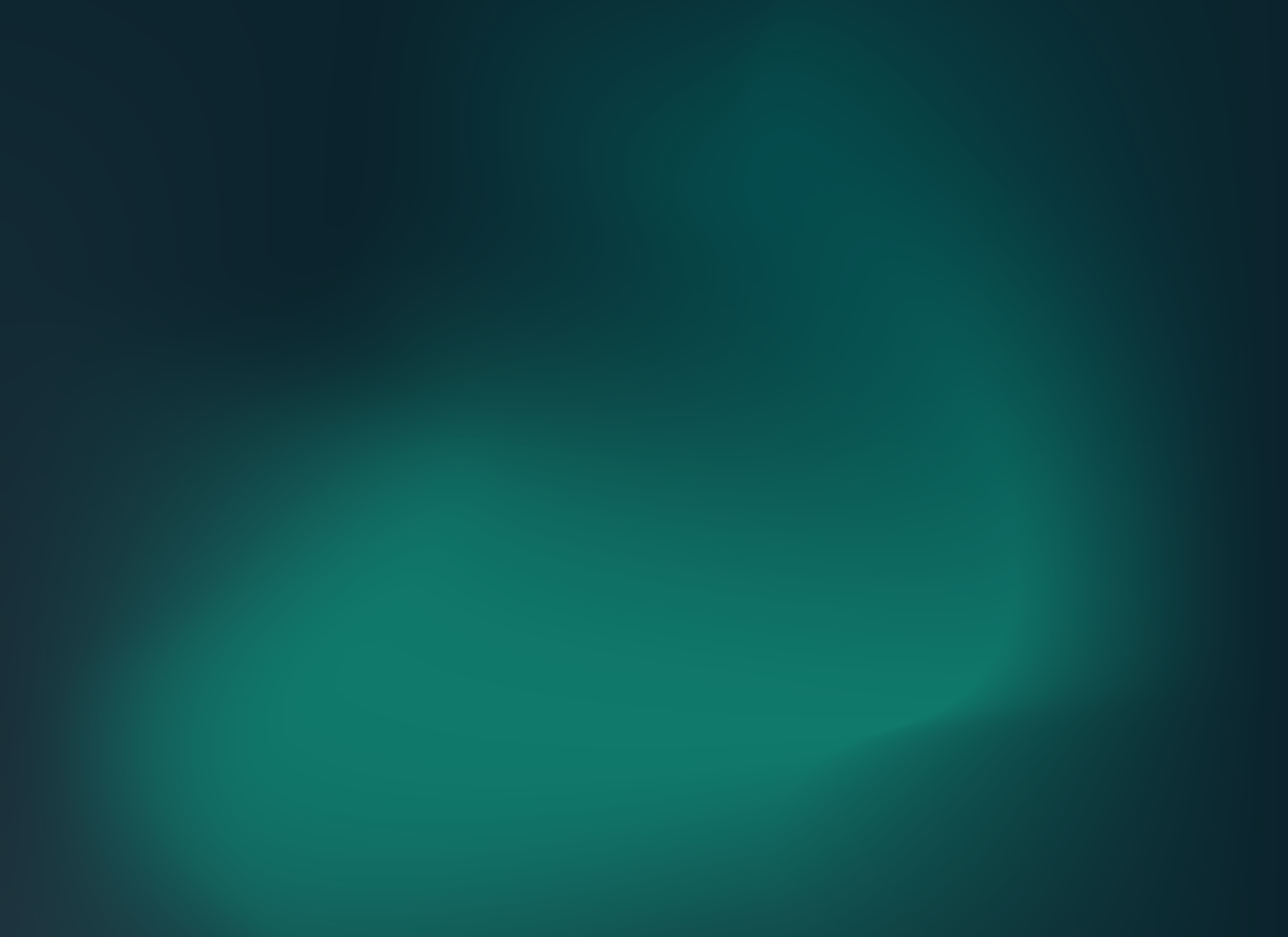
Case Study
Shutdown avoided utilizing 6” 150 class AOGV to replace leaking valves at Polyethylene plant in Texas
A Supermajor with a large modular facility in Texas was facing a process shutdown in their polyethylene unit due to inoperable ball valves on the flare line system. The Supermajor reviewed options to repair or replace the valves, but all required drainage of the immediate system, forcing a shutdown with significant HSE risks and financial impacts.
The Supermajor concluded that the Izomax AOGV mechanical isolation system, with their successful track record, and having used the AOGV technology successfully at another site, would be the most viable solution to preventing a shutdown.
Challenges
Volatile polyethylene systems require extremely safe, reliable, and robust solutions to mitigate all risks. When a Supermajor client faced issues with two inoperable ball valves, they turned to the Izomax AOGV mechanical isolation system. With the evaluation of the plant system, the Izomax AOGV process, and having a previous positive experience and a successful project outcome at a different site, the Supermajor’s technical specialists recommended Izomax for this critical application.
Solution
The customer began an in-depth application specific evaluation of the propriety Izomax AOGV mechanical isolation system, quality, safety, and procedures. Izomax staff visited the site for an application review to ensure a high degree of confidence among all parties.
A site survey was performed by Izomax shortly after initial meetings, ensuring access and space considerations could be digitally modelled and qualified as part of the job execution plans.
Izomax proposed a 6” 150 class AOGV which covered the pressure and temperature ratings required for the intervention. The 6” 150 system has been thoroughly tested and is approved by DNV as are all Izomax AOGV tools.
Prior to mobilization, a Factory Acceptance Test (FAT) was performed at Izomax facilities in Houston. The customer was present with technical Isolation specialists and site personnel throughout the FAT process. This ensured client specific qualification and witnessing adherence, as well as promoting detailed understanding of Izomax systems and processes by client plant personnel who would be on-site during the work phase.
Due to the low internal pipe pressure, hydraulic and mechanical separation of the flange pairs were required. In conjunction with the client, suitable points close to the flange pair were identified, with analysis performed to ensure that separation could be carried out safely and efficiently. Flange pair separation was successful and performed efficiently with no damage to the piping.
Outcome
Efficient completion of this project was critical. With two ball valves inoperable, and both passing, the refinery was facing a shutdown. The Izomax AOGV mechanical isolation tool offered a cost-effective solution whilst avoiding any interruption to the polyethylene process.
The entire operation including site survey, FAT and valve replacement at the refinery was flawless with no HSE incidents or non-productive time.
The project was completed ahead of time and on budget. Mobilization took place less than 5 weeks after receipt of the P.O. – project execution phase was planned to be 14 days, whilst the actual time used was 9 days for successful completion.
As with the vast majority of Izomax AOGV mechanical isolation work, no hot work was required, saving the operator considerable time and costs related to planning and executing hot work, in addition to mitigating complex HSSE risk.
System process and full pressure and flow integrity was maintained throughout the operation, with the plant returned to its original status and condition with two new ball valves in place.
The customer has already asked Izomax to look at other plant challenges at the same site based on the successful outcome achieved on this project.