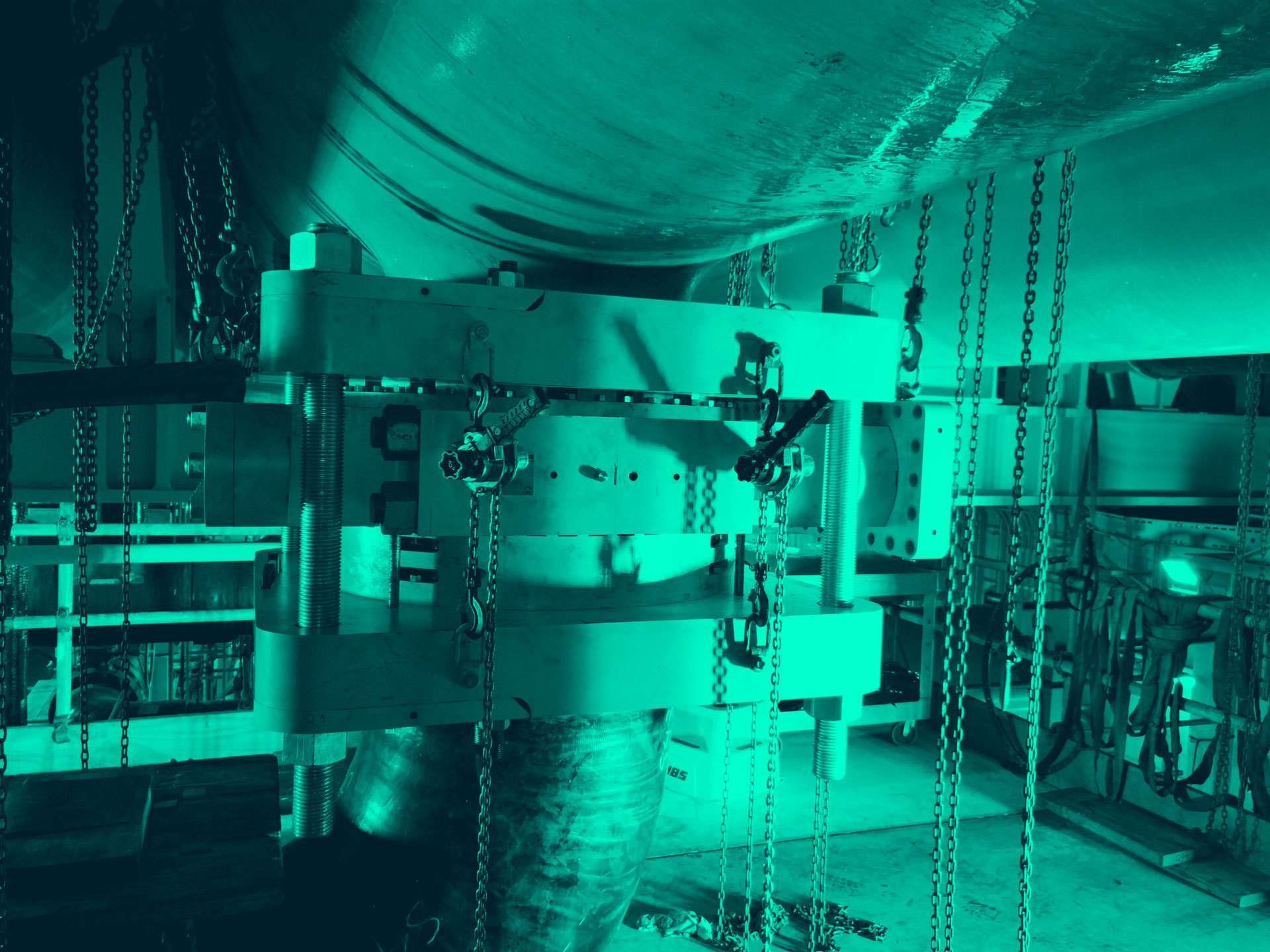
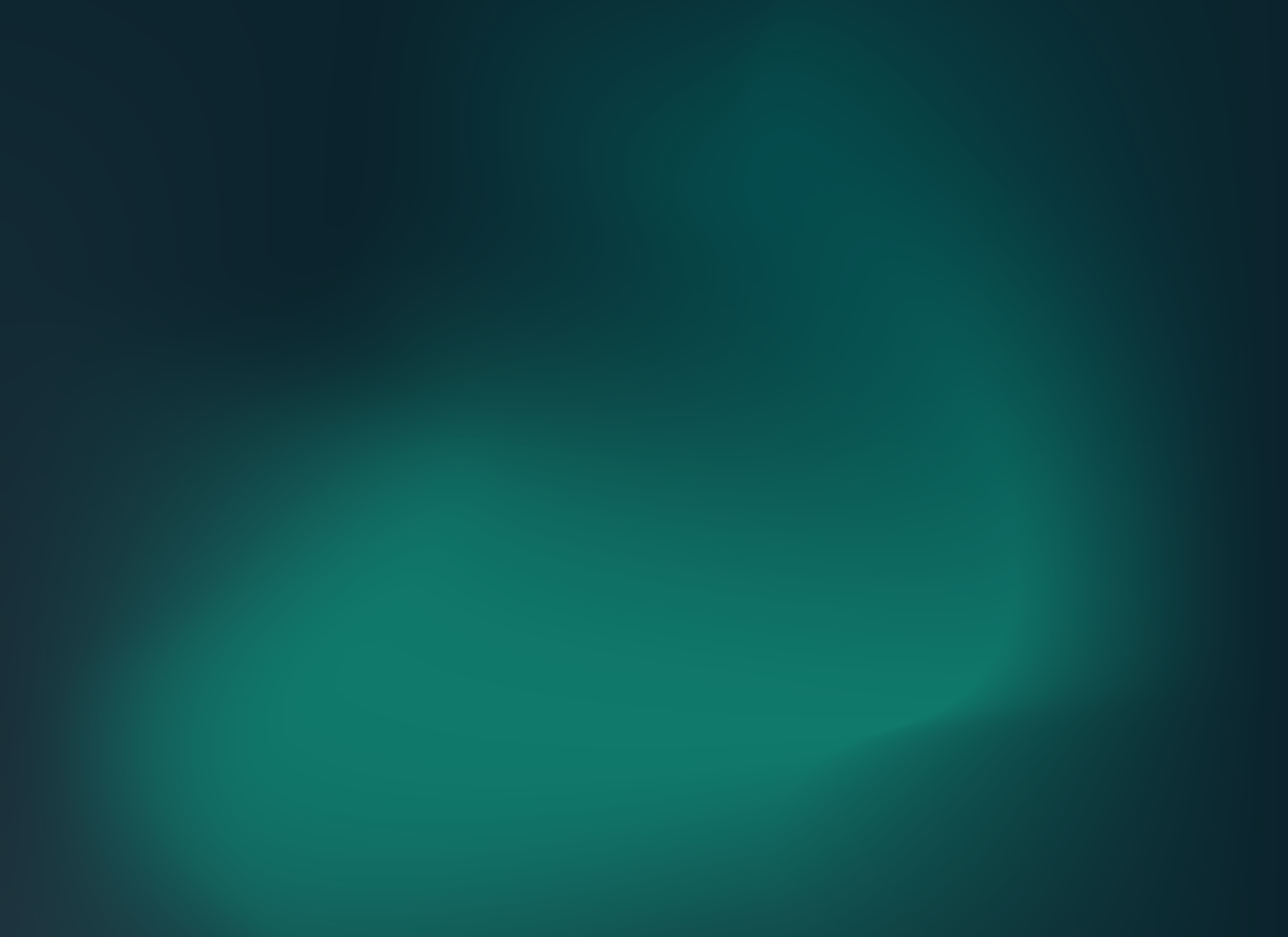
Case Study
Izomax performs first intervention in U.S. – Isolation of critical passing valve at refinery in Montana
A refinery Operator in the Montana region required a solution to address problems with their cooling water pumps. Their process requires one pump in continuous operation with a functional backup. In this instance, two of the three pumps had reliability issues with the third pump being inoperable. Due to the pumps being connected to the same main spools, initiating maintenance work was only possible by isolating at each of the valves. Traditional technologies were considered, but judged to likely require a partial plant shutdown and would require major changes to infrastructure including removing roofing. The Izomax AOGV mechanical isolation system was evaluated and selected to perform an on-site intervention.
Challenges
Critical utility systems such as nitrogen A passing valve was causing significant problems at a Montana refinery, where two out of three cooling pumps had reliability issues while the third was inoperable. The refinery was facing outages unless a suitable solution could be found. Furthermore, traditional interventions would require relatively major temporary changes to infrastructure, including removal of roofing, due to accessibility issues.
The client, a Supermajor, had not used the Izomax AOGV mechanical isolation system previously – meaning that a detailed evaluation of the AOGV technology, engineered solution and all processes and procedures would be required.
The application was a high temperature environment with 400 degrees F design temperature and internal pressure in the region of 725 psi. All three cooling pumps were connected to the same main spools, so initiating maintenance work was only possible by isolating the passing valve. An additional consideration was the asbestos gasket which would require careful handling and disposal.

Solutions
The customer began an in-depth evaluation of the propriety Izomax AOGV mechanical isolation system. The evaluation was based on strict requirements which needed to be met or exceeded prior to acceptance of the technology as a robust, safe and cost-efficient solution to the client’s challenges. The evaluation included the following steps:
Technical applicability
The Izomax AOGV needed to prove suitability for the application during reviews of the tool design, the valve location and mechanical integrity, spacing considerations, and material service conditions.
Track Record
Although the client only had one previous application of Izomax’s AOGV, and no applications in downstream refining, the AOGV had been thoroughly assessed by company engineers and was conditionally approved for use, contingent on an application-specific review by site engineers and corporate research staff.
Safety
The Izomax AOGV mechanical isolation system was vetted for site use by an interdisciplinary group consisting of engineering, process, mechanical and SHE specialists. Approvals were provided by site management based on the documented safety record of AOGV, site operator orientation training using materials provided by Izomax which was critical to understanding and being comfortable with the tool. Additionally, an Izomax site visit, and a mockup demonstration of the AOGV system showcasing the procedural nature of the AOGV install and the knowledge and experience of the Izomax personnel all fed into the evaluation approval.
Competing options
The nearest competing option for online isolation was identified to be a stopple, which was scoped for use and determined to be logistically very challenging to execute, at a cost ~2X that of an AGOV, and with a best-case confidence for success at 75%. The AOGV was assessed to be significantly easier to execute with a 100% success rate.
Schedule
Even with the additional time required for a custom fabrication, shipping, and the mockup demonstration, the AOGV was still competitive with the estimated timeframe required for use of a stopple given the execution hurdles that would need to be overcome.
The Izomax team performed a site survey in conjunction with the customer which included 3D scanning. Due to accessibility and space on site, the AOGV valve-side integrity clamp was redesigned to allow a safe and efficient operation. Izomax modified an existing 6 inch 300# tool to allow for the pressure and temperature ratings required for the intervention. The new 6” 400# AOGV was thoroughly tested and approved by notified body DNV, as are all Izomax AOGV tools. As a result, the customer concluded that Izomax have robust technologies, processes and procedures which would be suitable as a solution.
Outcome
Efficient completion of this project was critical. With one of three pumps inoperable, and the other two pumps carrying reliability problems, the refinery was facing outages. The Izomax AOGV mechanical isolation tool provided the most cost-efficient solution. Fundamentally, the AOGV mitigated the requirement to make major changes to plant infrastructure at significant cost and risk.
The entire operation including site survey, manufacture, testing and execution at the refinery was flawless with no HSE incidents or nonproductive time.
As with the vast majority of Izomax AOGV mechanical isolation work, no hot work was required, saving the operator considerable time and costs related to planning and executing hot work, in addition to mitigating complex HSSE risk. The asbestos identified in the existing gasket was safely disposed of, with an approved decontamination process performed on site. System integrity was maintained throughout the operation, with plant returned to original status and condition.
The Izomax team enabled an estimated cost saving of up to $10m USD as estimated by the client because of avoiding a partial plant shutdown.
The customer has placed repeat orders with Izomax based on the outcomes achieved on this first refinery operation in the U.S.A.