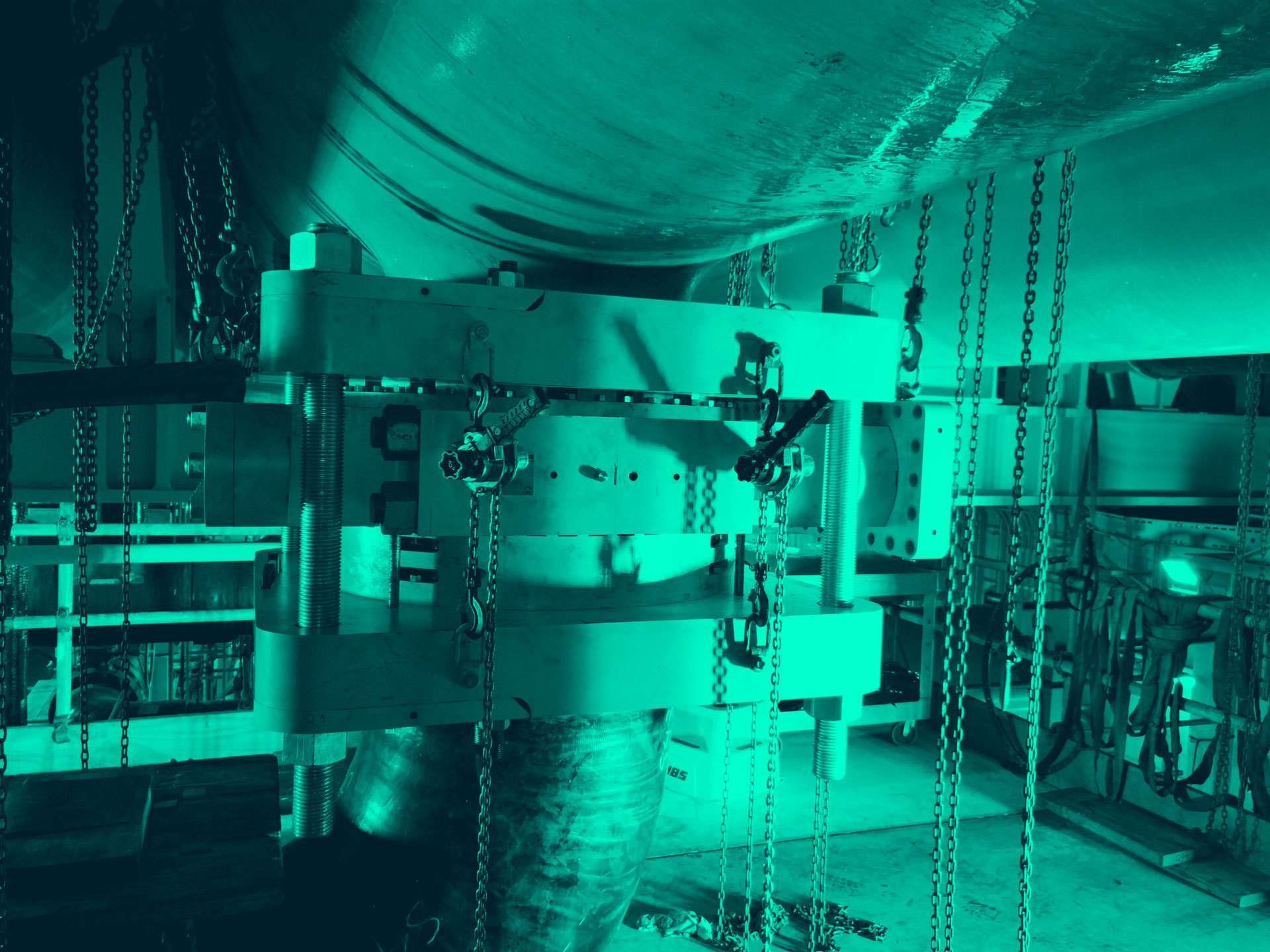
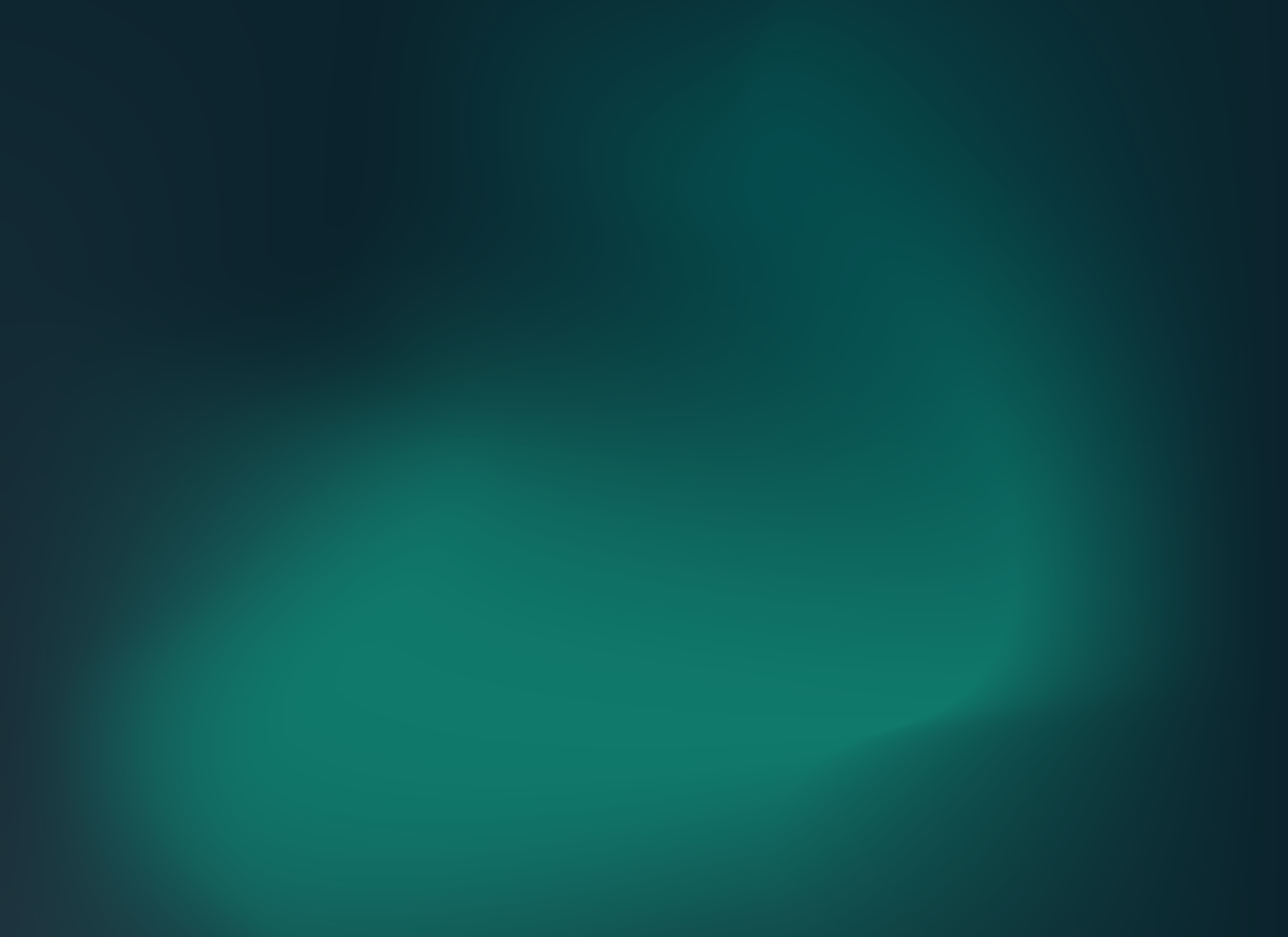
Case Study
New Izomax DN600 & DN250 AOGV systems designed for GRE deployed at a semi-submersible production platform supplying gas to amajor LNG facility
A major customer in Western Australia had experienced fouling in their heat exchanger seawater cooling systems due to faulty seawater filters. The fouling led to a significant reduction in system cooling capacity. The customer was planning for a production increase on the semi-submersible production platform, which meant they would need an increase in cooling capacity. In order to avoid a shutdown to repair the fouling problem, an intervention using a DN600 AOGV was considered as a viable option.
The same customer also had issues with passing butterfly valves on their seawater HVAC systems. A DN250 10” butterfly AOGV was looked at as an option to replace the valves outside a planned shutdown.
The Izomax patented AOGV is a mechanical isolation tool which can set and retract a blind spade, or a butterfly valve, between a pair of flanges on a pressurised process system. The blind spade or a combination of several spades in different locations can facilitate the replacement of valves and pumps. The AOGV can also be used to take a vessel out of a closed loop temporarily for safe entry and bringing it back on-line whilst the main process is kept in operation continuously.
The two scopes described above planned for the installation of eight isolation spades with the DN600 AOGV, as well as replacing four butterfly valves with the DN250 AOGV.
The facility is one of the region’s largest suppliers of LNG. Bearing in mind the global energy requirements, and current supply issues, any extended production outage was detrimental to the client and their customers.
When reviewing Izomax’ proposals and comparing to alternative solutions, the client saw the possibility of reducing the planned shutdown while the utility systems were kept operational.
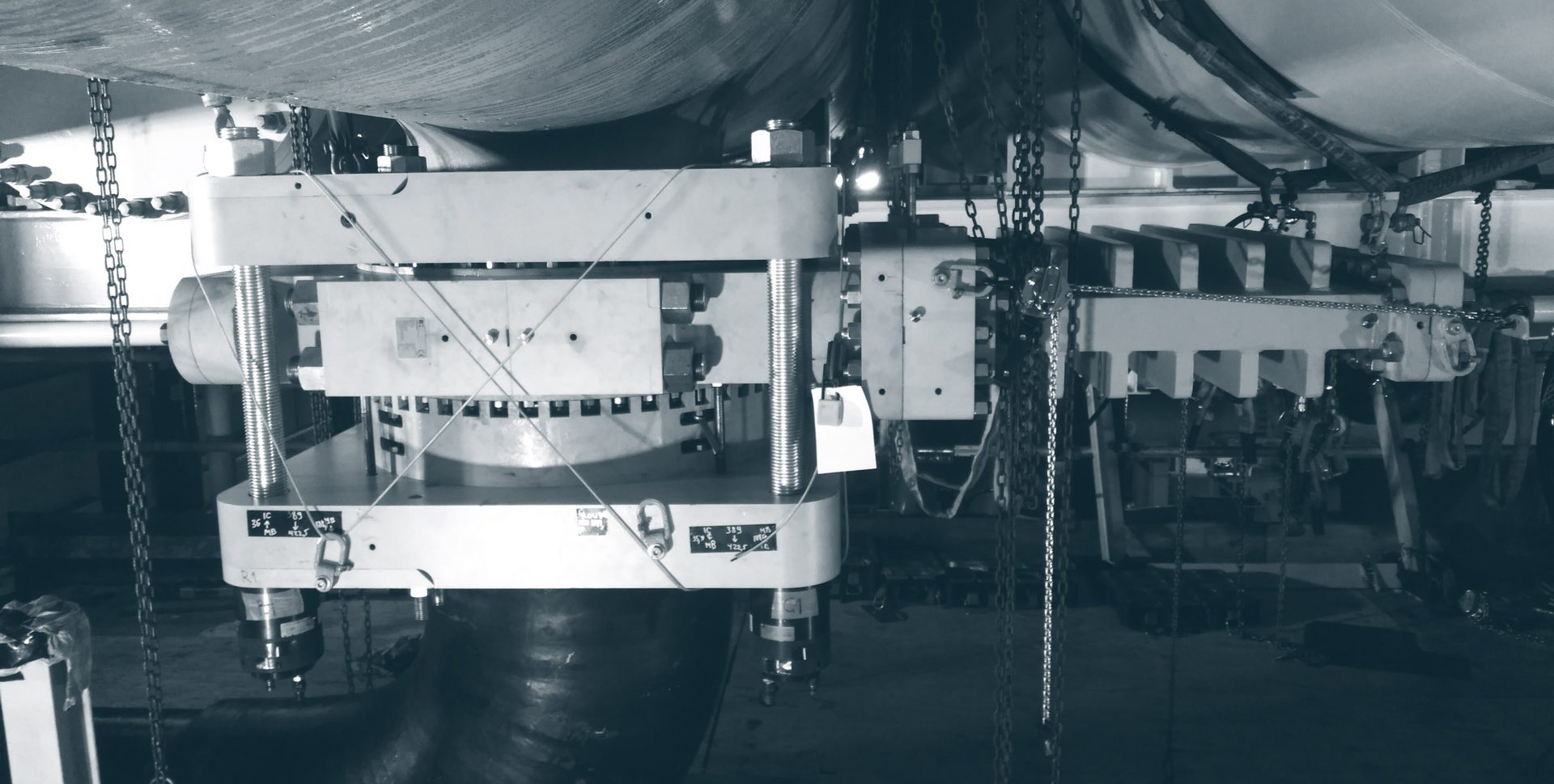
Challenges
Izomax has successfully performed AOGV operations for this client, but this was the first operation on glass reinforced epoxy (GRE) piping. GRE piping is quite different to steel equivalents, primarily used for its corrosion resistance and light weight. There are several challenges to be considered when planning an intervention with the AOGV mechanical isolation system on GRE piping, including:
- GRE is an Amorphous material with relatively high surface rugosity
- Water can diffuse/permeate through the glass fibre layers/windings, particularly in bolt holes on flanges
- The outer diameter of the flanges is un-even in GRE piping, as are flange shapes and dimensions
- Structural capacity of GRE is generally lower than steel
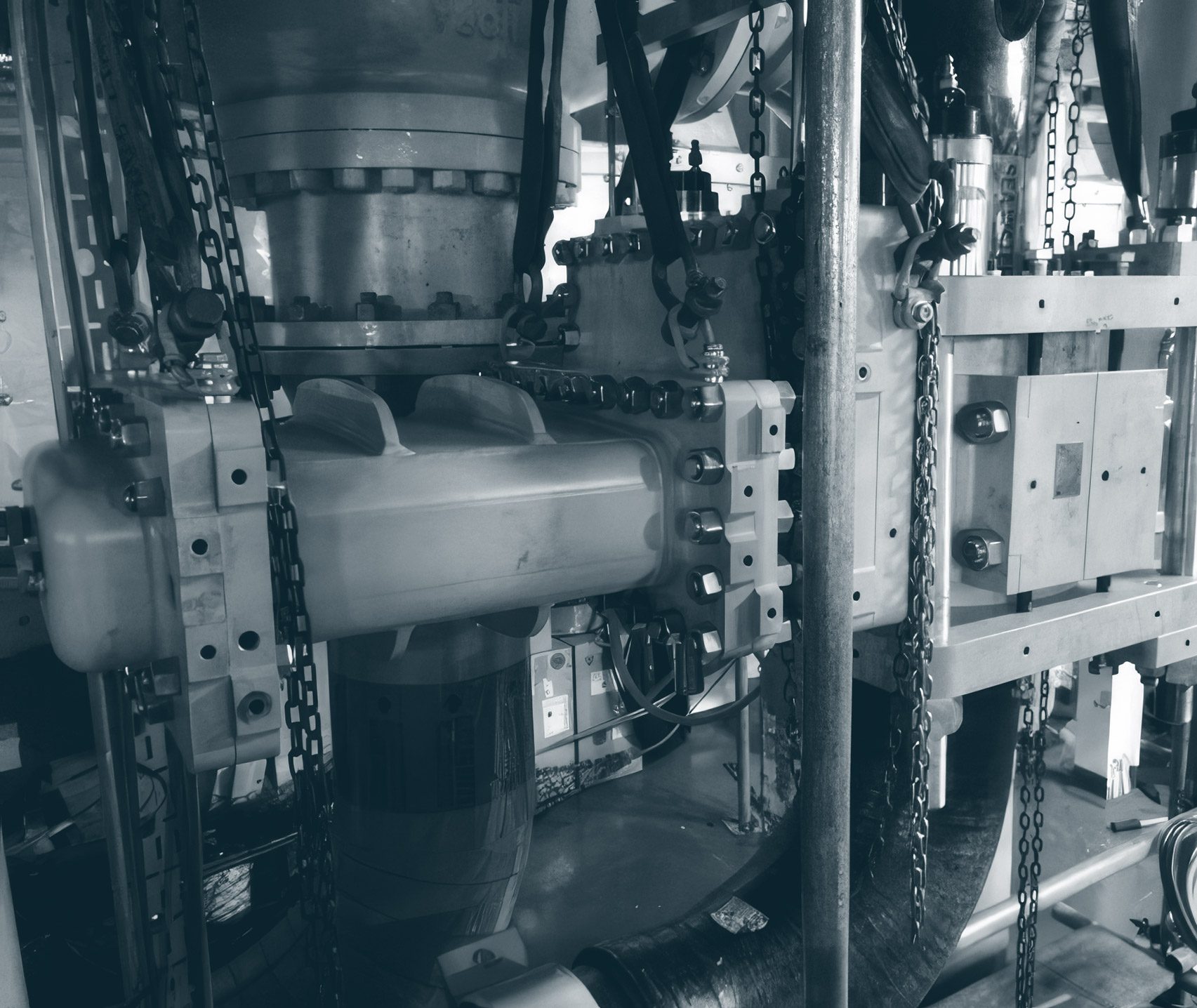
Testing, Planning and Preparing
The Izomax engineering team redesigned several aspects of the AOGV mechanical isolation system to ensure compatibility with GRE and ensure any challenges could be safely mitigated. All approved design changes were manufactured to exacting standards, and then subjected to an extensive workshop testing program.
The testing process was performed on GRE piping and ancillaries provided by the customer to ensure that the system would work in a real-world environment on like for like piping.
The testing process included new elastomers with varying shore hardnesses, ensuring a conformable seal despite GRE rugosity. New AOGV flange bolt replacement plugs were tested to mitigate the fluid permeation seen on flanges. The AOGV design changes included clearance changes to allow for the GRE unconformities. Backup rings of various thicknesses were designed so that unexpected GRE unconformities could be covered whilst still maintaining an acceptable elastomer seal extrusion gap between the sealing surface (GRE) and elastomer seals.
Because GRE has very different mechanical properties to steel of similar dimensions, the AOGV system was tested at lower torque (ensuring sealing qualification without exerting excessive structural stress on GRE piping/spools/flanges).
Testing protocols were refined throughout the program, with learnings transferred to necessary improvements which were then re-tested. Once a robust system was in place, repeat testing took place to verify results.
New Procedures were developed for the GRE compliant AOGV to ensure successful on-site job execution.
The customer was present throughout the assembly and testing program, formally witnessing the entire process.
The design of the AOGV meets or exceeds the requirements of the Pressure Equipment Directive (PED), following the unfired pressure vessel standard EN 13445. The AOGV design is verified by FEM/FEA (Finite Element Analysis) on each individual unit. The AOGV’s conformity to the regulations, directive and standard is assessed by DNV, this includes review of the design calculations report; review of material selection; follow-up of production; welding; material traceability, and proof testing.
Site Operation
The team that performed system checks and prepared the equipment in the workshop prior to shipping also performed the operation on-site, ensuring continuity from planning, preparation, testing and final job execution.
Due to multiple personnel working simultaneously in a relatively confined space, the coordination of activities had to be well planned.
The AOGV mechanical isolation system was installed and operated by a team of three trained Izomax
Outcome
The entire operation was completed without any incidents and to the client’s full satisfaction. The Izomax AOGV team executed work on critical systems without interfering with the other activities on the installation. As with all Izomax AOGV mechanical isolation work, no hot work was required, saving the operator considerable time and costs related to planning and executing hot work, in
addition to mitigating complex HSSE risk. System integrity was maintained throughout the operation, with plant returned to original status and condition.
After the successful execution of this relatively complex project, the customer has ordered several new AOGV systems in various sizes. Izomax has successfully tested each of the new systems, which are now ready for deployment. The New AOGV designs cover GRE to GRE as well as GRE to Steel weld-neck flanges and GRE to Lap-joint flanges.