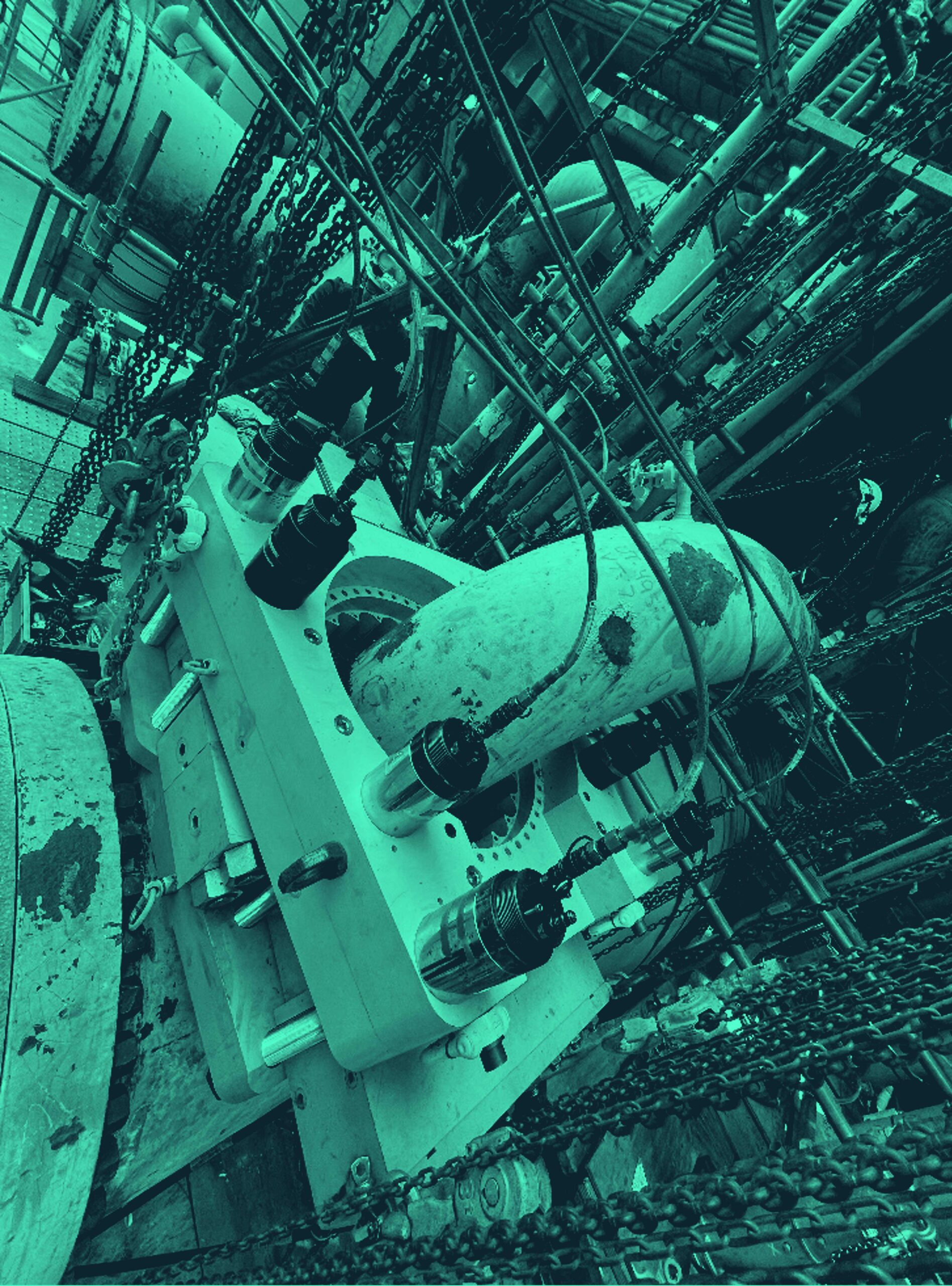
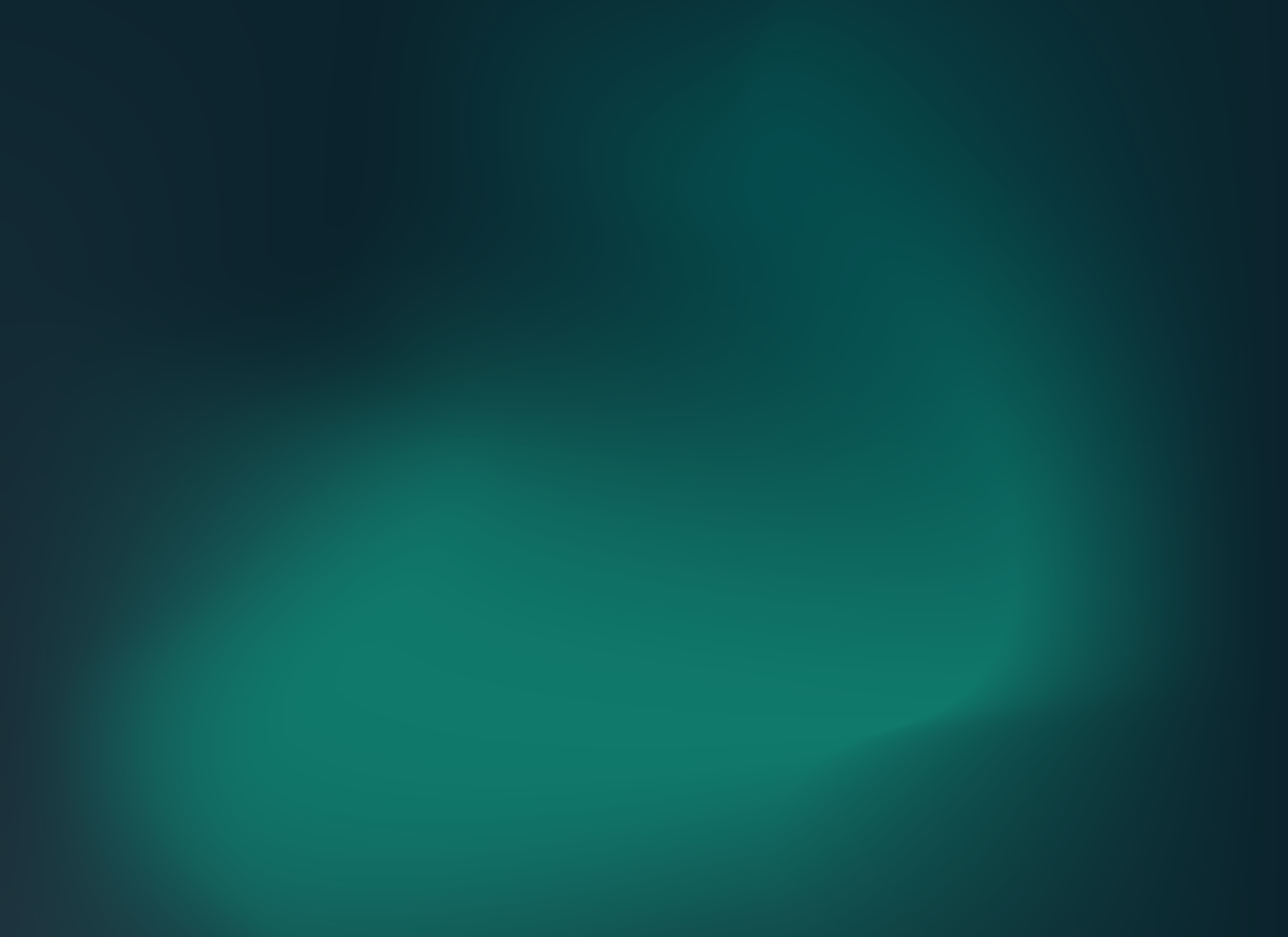
Case Study
Capacity restored at one of the world’s largest refineries to safely repair heat exchange bundle without shutdown
A Supermajor was facing continued process flow reduction at a major refinery in the USA caused by blockages in a heat exchanger bundle.
Bypass lines were in place enabling a second heat exchanger to provide a degree of additional support, but capacity was still far from optimal.
The refinery operator, having considered all available options for intervention and repair, selected the Izomax AOGV mechanical isolation system as the preferred choice for positive isolation without a shutdown.
Challenges
The heat exchanger bundle was clearly in need of overhaul, with a differential pressure in the region of 40 psi measured across the inlet / outlet. The system was known to be flowing, but without physical flow meters in place only calculated values were available.
Complete isolation of the heat exchange system was required to allow safe access for cleaning and system overhaul. With the 18” charge gas inlet and outlet and 12” Propylene outlet line sizes, two different AOGVs would be required.
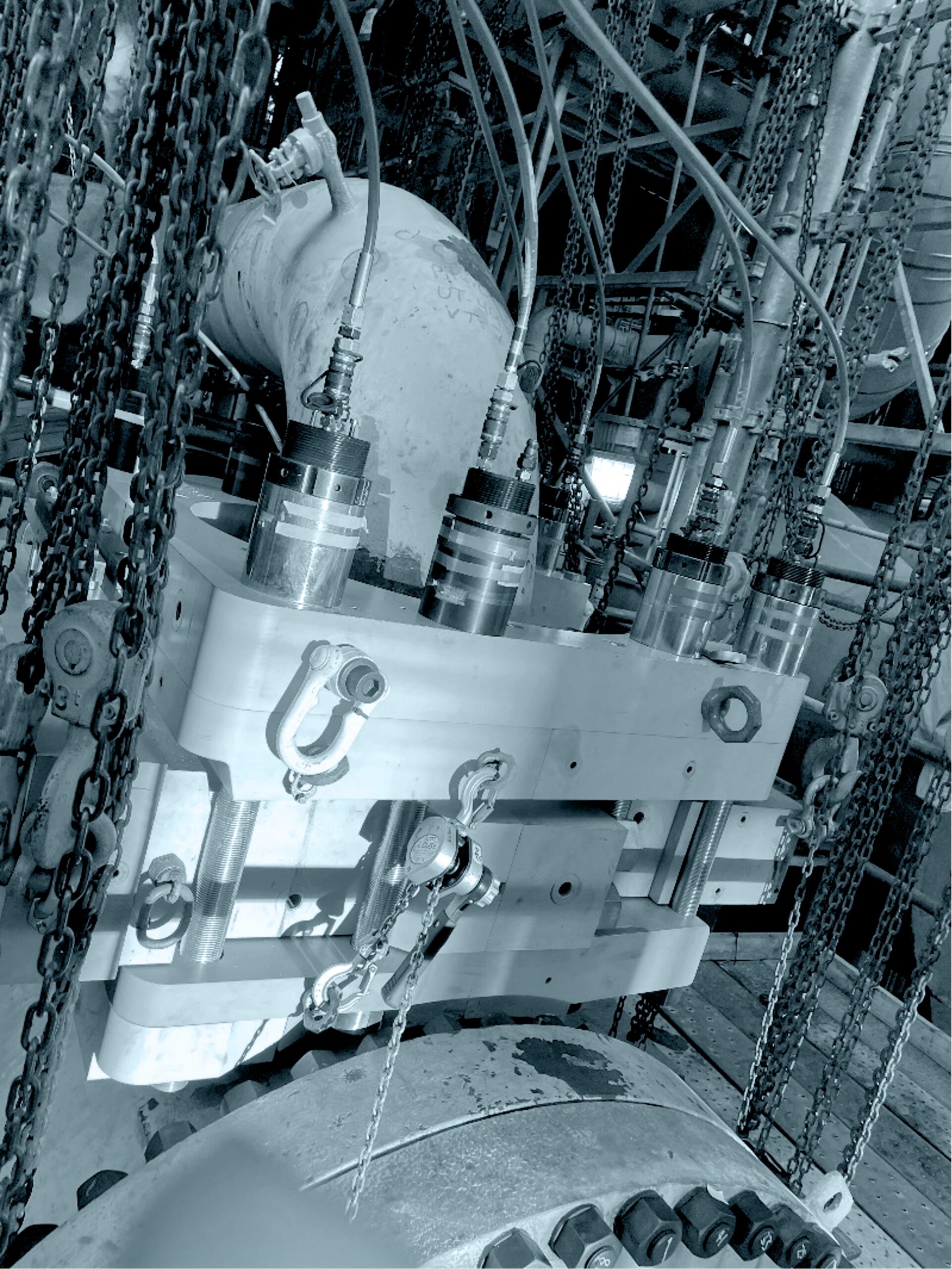
Solutions
Having previously worked with the customer on numerous projects, the Izomax team had a detailed understanding of the expectations regarding safety, engineering and operational processes and procedures. Dialogue with the customer on-site team was continuous, and well documented, to ensure a successful outcome on this complex intervention.
To ensure dimension and spatial restrictions could be met, Izomax performed a site survey, with 3D scanning to provide digital input to the modelling software.
Without valves in place, there was no way to stop the ongoing inlet charge gas flow through the system without a shutdown. Whilst the AOGV has been utilized in systems with low flow rates, calculated flow was uncertain.
The client agreed to Izomax’s proposed solution: A modified design to the AOGV spade, with bespoke hydraulic pistons designed to provide centralization of the spade under flow conditions.
The client was an integral part of the design process, from initial criteria through to acceptance. Prior to mobilization, a Factory Acceptance Test (FAT) was performed at the Izomax facilities. The customer was present with technical Isolation specialists and site personnel throughout the FAT process. This ensured client specific qualification and witnessing adherence. Furthermore, it enabled client plant personnel, who would be on-site during the work phase, to develop a detailed understanding of Izomax systems and processes.
Outcome
Despite the complexity and challenges envisaged whilst planning the operation, a successful outcome was deemed critical to restoring plant capacity without a shutdown.
The Izomax AOGV mechanical isolation system was specifically selected for the intervention, based on the customer’s previous experience on several projects. Agreed design changes to the AOGV spade, incorporating hydraulic pistons to aid spade centralization, were implemented in the planning process to mitigate flow conditions.
The operational sequence was followed according to the agreed plan, with the 18” charge gas inlet flange isolated. With the AOGV spade left in place, the AOGV tool was moved to the 18” charge gas outlet. Once isolation was confirmed on the outlet, the AOGV was left in place and a new AOGV was used to isolate the 12” propylene outlet. Full day and night crews were mobilized to minimize on-site time.
Extensive leak tests were performed prior to the customer on-site personnel removing the dollar side plates on the heat exchanger bundle. The system was hydro-jetted and checked to ensure full capacity would be restored. After the cleaning process was complete and the heat exchanger was re-assembled, Izomax charged the system with Nitrogen and performed a full post-assembly leak test. To avoid process medium contamination, the Nitrogen was purged utilizing the bespoke AOGV manifold, and replaced with the process medium.
A final leak test was successfully performed. The AOGVs and spade were removed (with new flange gaskets inserted), and the site was returned to full working order.
The job was completed successfully, without HSE incidents.
As with the vast majority of Izomax AOGV mechanical isolation work, no hot work was required, saving the operator considerable time and costs related to planning and executing hot work, in addition to mitigating complex HSSE risk.
Due to the complexity of the project, an Izomax team has documented a performance improvement opportunity which is being presented to the customer. This aims to implement lessons learned, ensuring continuous improvement on future projects.