This website uses cookies so that we can provide you with the best user experience possible. Cookie information is stored in your browser and performs functions such as recognising you when you return to our website and helping our team to understand which sections of the website you find most interesting and useful.
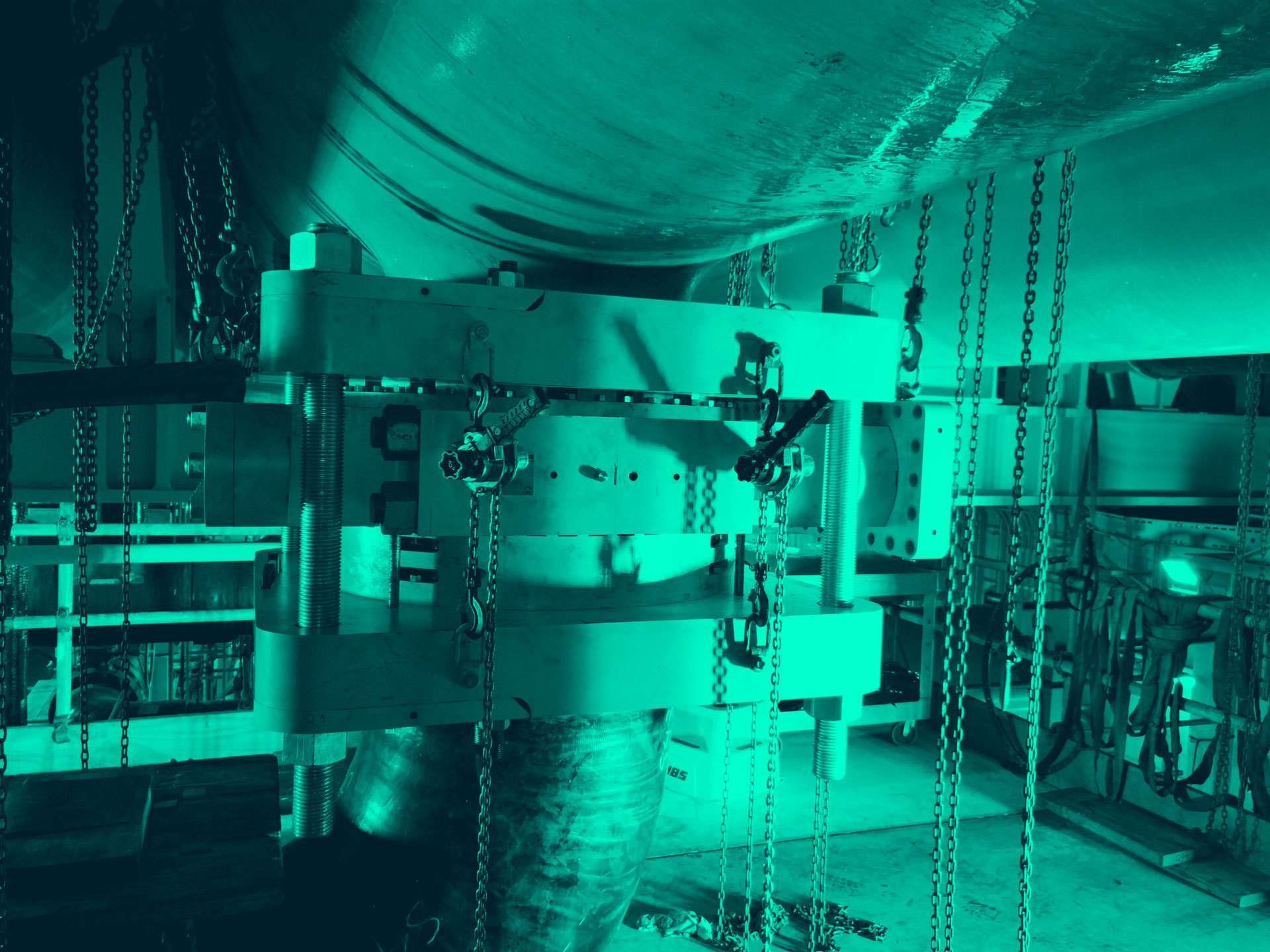
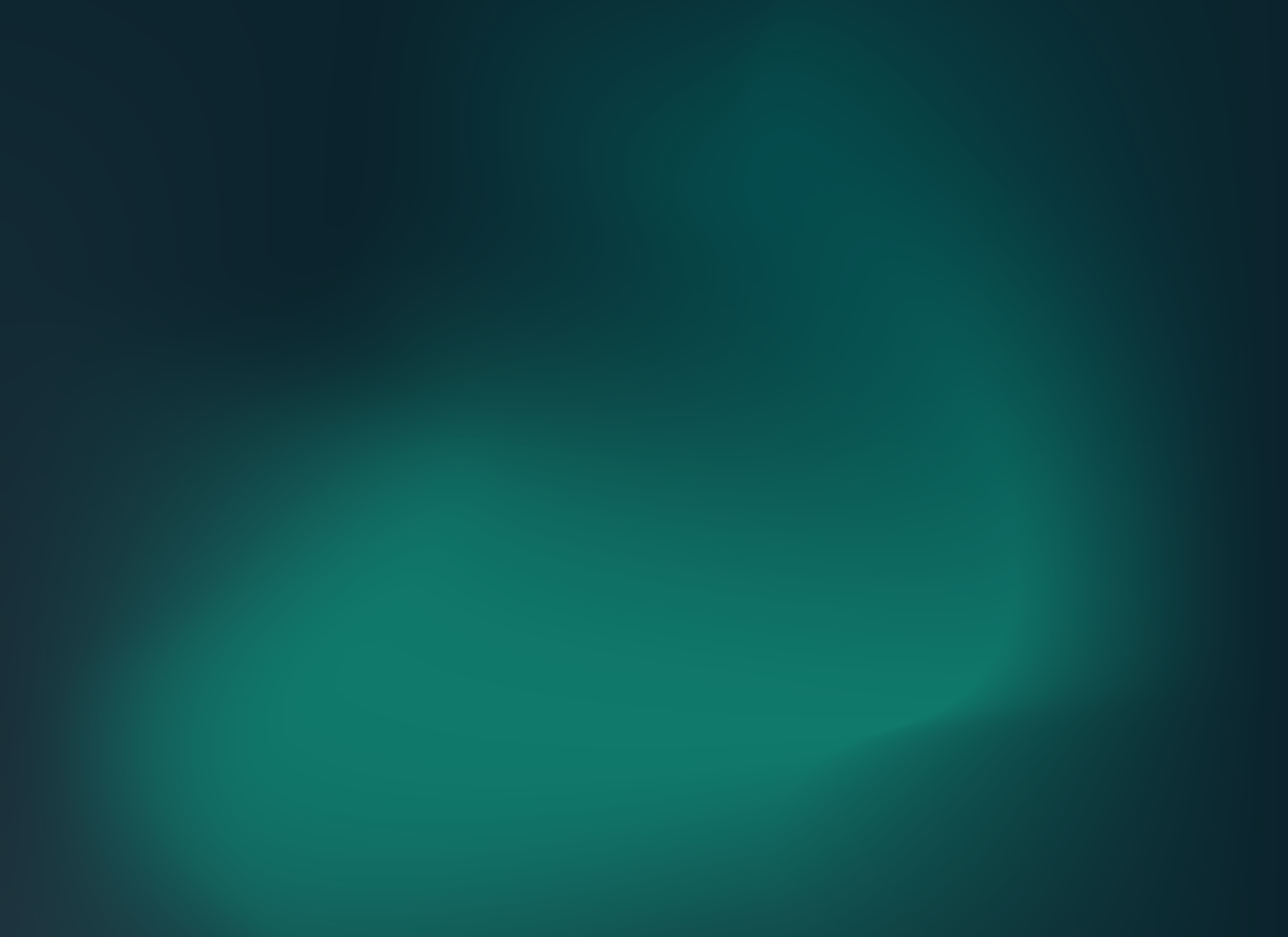
Case Study
Flexible, responsive: Valve repair & replacement
A platform operator in the Norwegian North Sea had a problem with a passing valve related to the second stage separator containing hydrocarbons at 90 bar (1300 psi) and 75 degrees C (165° F). From initial enquiry, Izomax designed, engineered and implemented a solution in just eight weeks, with no loss of productive time. The Izomax AOGV mechanical isolation tool was tested, certified and CE marked prior to mobilisation.
Challenges
Oil and gas prices were averaging over 100$ per barrel, and the energy security situation was acute in the spring of 2022. A solution was urgently needed to allow production to continue on an important producing platform – avoiding the major costs, risks and complex operations associated with a shutdown and draining of the inventory. There were no usable isolation points near the valve in question, and there was no possibility to use a bypass line due to passing valves. The line was a crude oil line with high temperature and pressure. A key element of any approach was to minimize or avoid a shutdown.
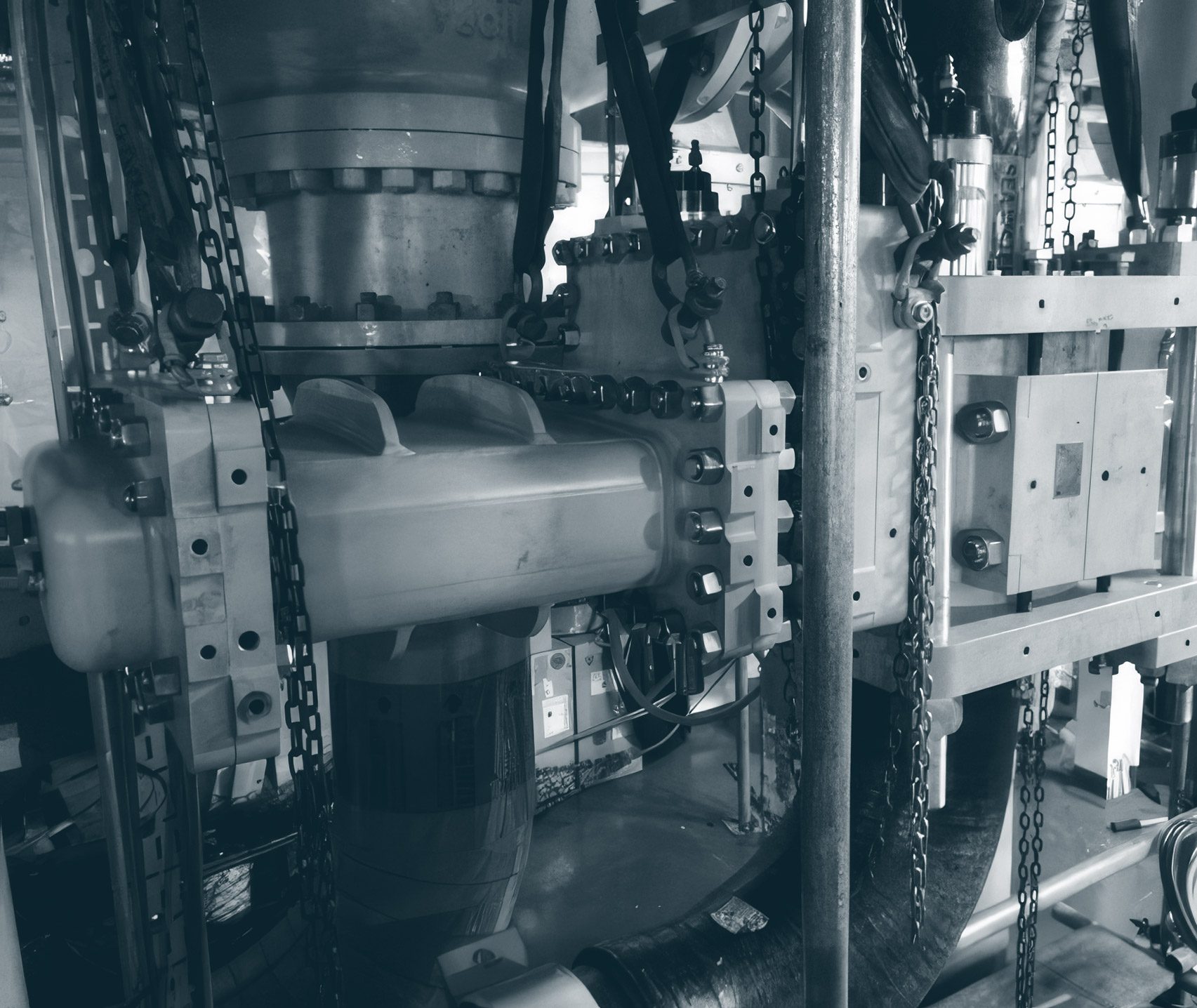
Solutions
The Izomax patented AOGV is mechanical isolation tool which can set and retract a blind spade in a pair of flanges on a pressurised process system. The blind spade or a combination of several spades in different locations can facilitate the replacement of valves and pumps. The AOGV can also be used to take a vessel out of a closed loop temporarily for safe entry and bringing it back on-line, whilst the main process is kept in continuous operation. set in between the valve and pipe spools leading to the second stage separator.
Testing, planning & preparing
Izomax conducted an on-site survey, including a high precision 3D scan, allowing us to create an AOGV system which was 100% aligned to the flanged valve. With obstacles on both sides of the passing valve, the AOGV mechanical isolation tool was specially designed and manufactured to fit around a parallel 1 inch valve and blind flange on one side, in addition to a 6 inch valve located on the other side of the valve. As the 6 inch CL900 line had a ring joint as the sealing element, the AOGV was equipped with a bespoke removal tool. This enabled the ring joint to be removed from the ring joint groove, without coming into contact with the groove itself, thus avoiding any damage to the sealing surface.
The AOGV system was also equipped with a special insertion tool, enabling a new ring joint to be inserted into the groove when restoring the system, allowing the flanged connection to be compressed against the new ring joint, avoiding contact with the insertion tool. Despite the system’s operational pressure not exceeding 89 bar (1290 psi) throughout the operation, the AOGV mechanical isolation tool was verified at 1.43 x design pressure (143 bar/ 2075 psi) prior to mobilisation, to ensure no leakages in the event of pressure build-up.
Site operation
The AOGV’s isolation spades were set on each side of the leaking valve, creating a hydrocarbon and pressure freed valve cavity. The valve was discovered to be in far worse condition than anticipated, hence Izomax was tasked with creating a solution to completely remove the valve from the system and replace it. Within seven days, the Izomax team designed, manufactured and tested three bespoke isolation spades with integral bleed ports, to facilitate replacement of the passing valve from the line. The three spades were installed upstream, downstream and on the valve itself, in a complex operation where cavities had to be hydrocarbon and pressurefreed through the AOGV mechanical isolation tool or the special isolation spades.
Outcome
The fundamental objective of the operation – to safely avoid any loss of production – was met, despite the unforeseen challenges with the condition of the valve. The entire operation was executed without any HSSE incidents or non-productive time. Izomax provided the fully engineered and certified isolations to enable the initial in-situ repair of the passing valve. When the valve proved to be beyond repair, we acted with speed and flexibility to provide an additional solution which would safely remove and replace the valve, whilst normal production levels continued. Without the Izomax AOGV mechanical isolation system, a shutdown would have been inevitable. The length of any shutdown and loss of production would have increased significantly, when the need to replace the valve became clear. By mitigating the initial requirement for an unplanned shutdown, the Izomax AOGV mechanical isolation tool further assisted productivity by allowing a “hidden” issue to be solved whilst operations and production continued. Ultimately, use of the Izomax AOGV mechanical isolation system saved the operator an estimated $46million USD.