This website uses cookies so that we can provide you with the best user experience possible. Cookie information is stored in your browser and performs functions such as recognising you when you return to our website and helping our team to understand which sections of the website you find most interesting and useful.
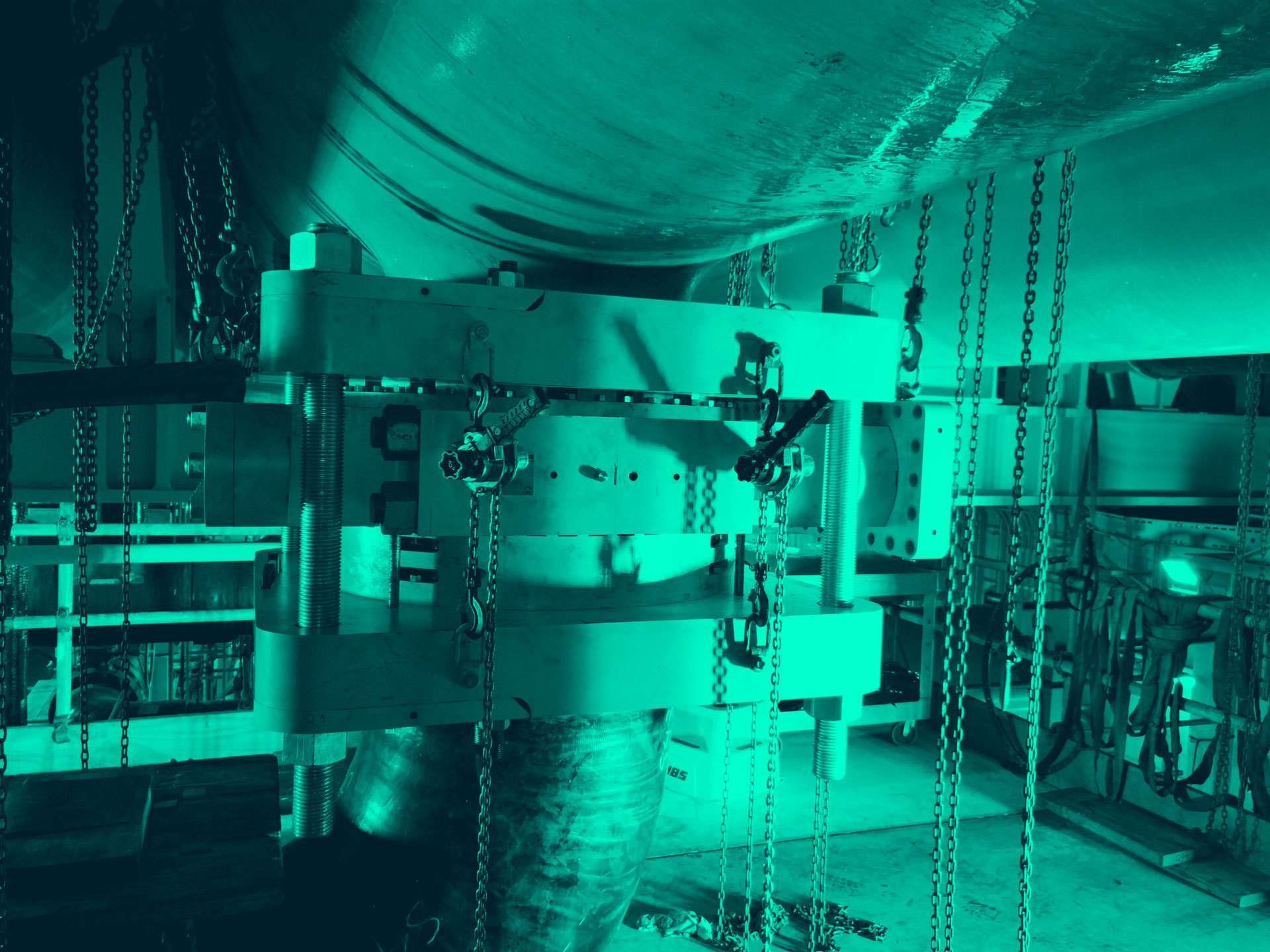
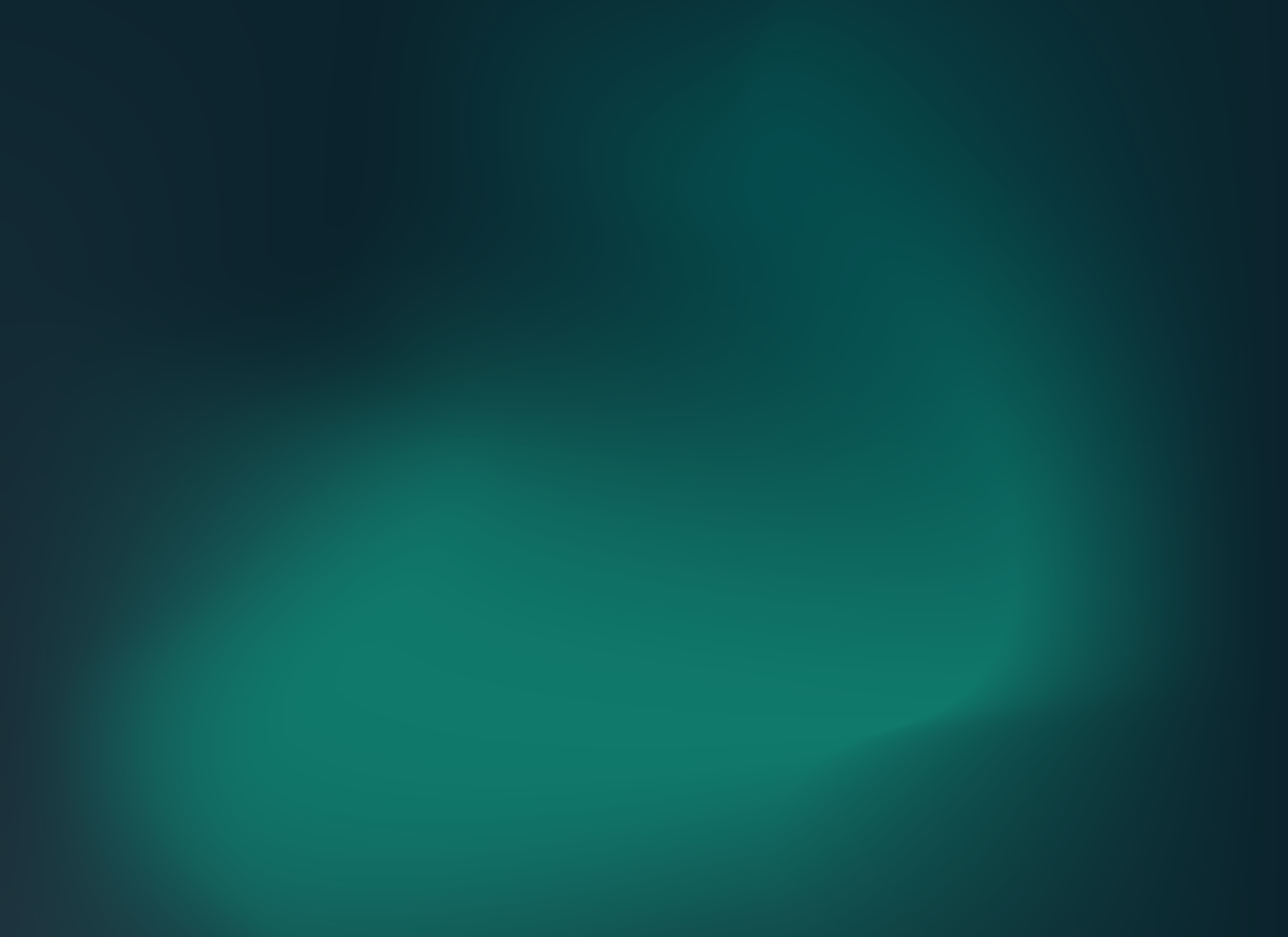
Case Study
Cryogenic AOGV system eliminates facility shutdown
The drain line from the flare knockout drum on an LNG re-gasification plant needed to be replaced during operation. By designing and manufacturing two cryogenic AOGV mechanical isolation tools, Izomax enabled maintenance and modification to be carried out on a complex facility with many dependencies and few redundancies. Uptime was secured throughout the entire operation.
Challenges
The operator of a major gravity based offshore LNG re-gasification plant needed to perform maintenance which involved replacement of a pipe section. The maintenance location was by the flare knockout drum, close to where natural gas is cooled to -162°C. Typically, this type of operation is performed using isolation points built into the facility. However, there were no suitable isolation valves near the maintenance point. Integrity requirements ruled out legacy isolation methods leaving a facility shutdown as the most likely pathway to enable the necessary maintenance.
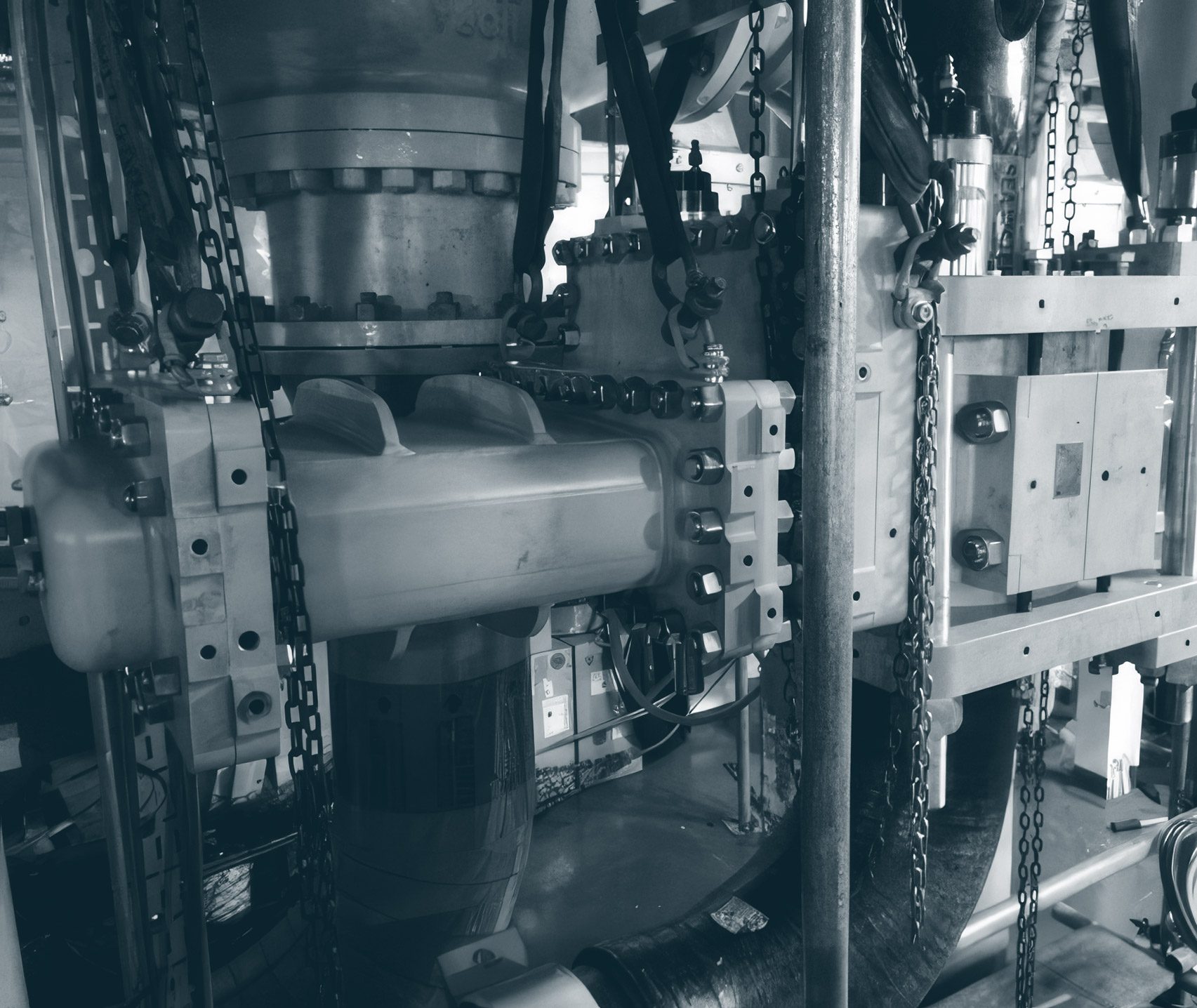
Solutions
The Izomax patented AOGV is a mechanical isolation tool which can set and retract a blind spade in a pair of standard flanges on a pressurised process system. The blind spade or a combination of several spades in different locations can facilitate the replacement of valves and pumps. The AOGV can also be used to take a vessel out of a closed loop temporarily for safe entry and bringing it back online, whilst the main process is kept in continuous operation. chosen for installation upstream on a knockout drum nozzle, as well as downstream on a drain line, thereby isolating a section whilst the main process could continue.
Testing, planning and preparation
Two 3 inch ASME Class 150 Cryogenic rated AOGVs were commissioned for the work scope.
Working closely with the operator, Izomax planned for site activities including pipe spool and valve replacement whilst the main process was running. Following manufacture, the AOGV mechanical isolation tools were subject to extensive workshop testing, verified by DNV to ensure regulatory compliance. Detailed operations planning included logistics, HSE, HAZID, lifting and rigging.
Site operation
The Izomax equipment and crew mobilised on schedule, enabling on-time operations during which the AOGV mechanical isolation tools provided a zero-energy zone, enabling a complete replacement of the pipe spool in addition to replacing a valve, without any downtime.
Outcome
The Izomax engineering and support team worked closely with the customer to operationalize the proposed cryogenic solutions. The entire operation including site survey, manufacture, testing and onshore on-site work was flawless with no HSE incidents or non-productive time.
As with the vast majority of Izomax AOGV mechanical isolation work, no hot work was required, saving the operator considerable time and costs related to planning and executing hot work, in addition to mitigating complex HSSE risk. System integrity was maintained throughout the operation, with plant returned to original status and condition. Both isolations were performed as planned with the two tools provided, saving the operator a shutdown estimated at 14 days with a value of approximately $20m USD per day.