This website uses cookies so that we can provide you with the best user experience possible. Cookie information is stored in your browser and performs functions such as recognising you when you return to our website and helping our team to understand which sections of the website you find most interesting and useful.
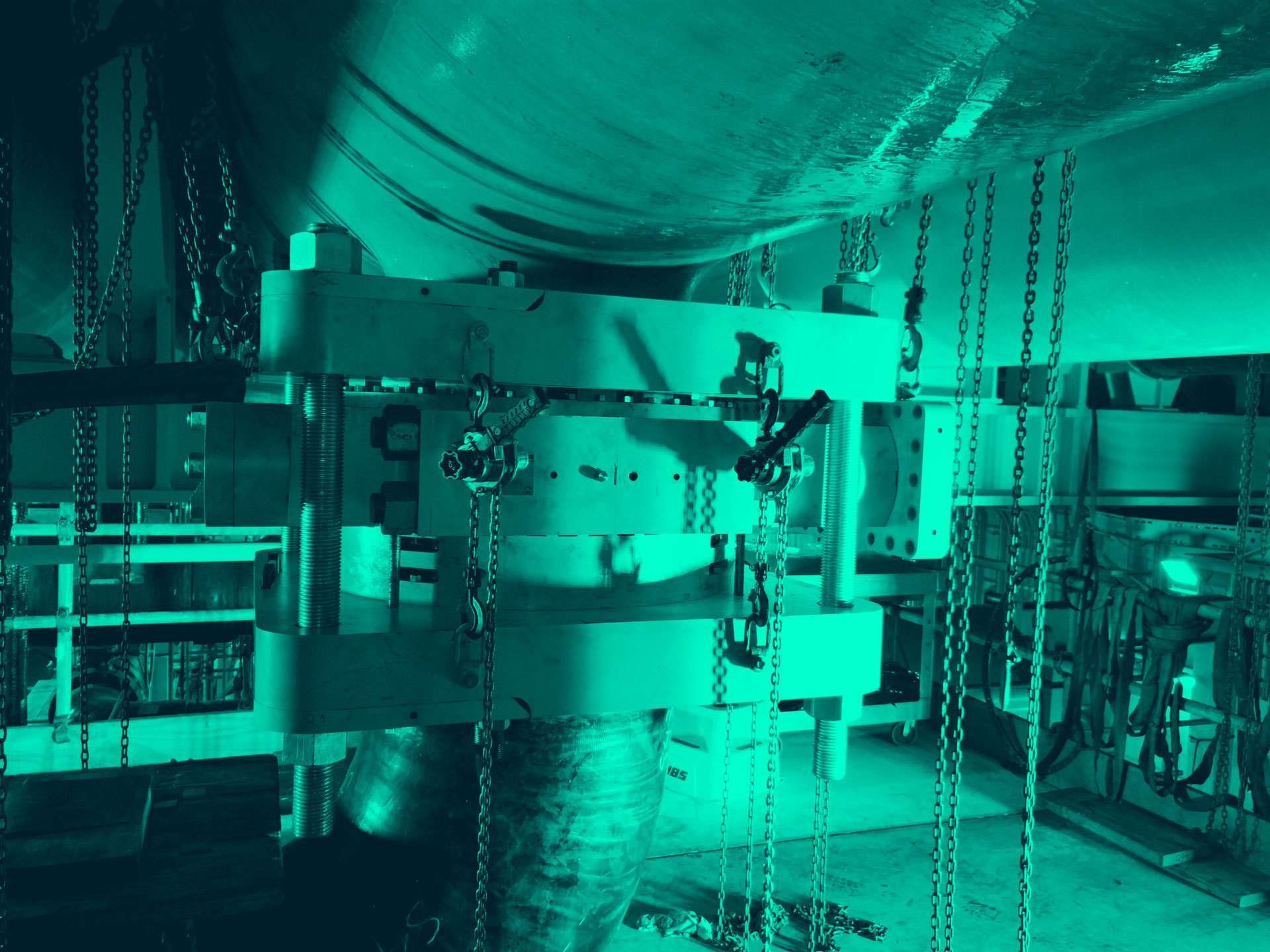
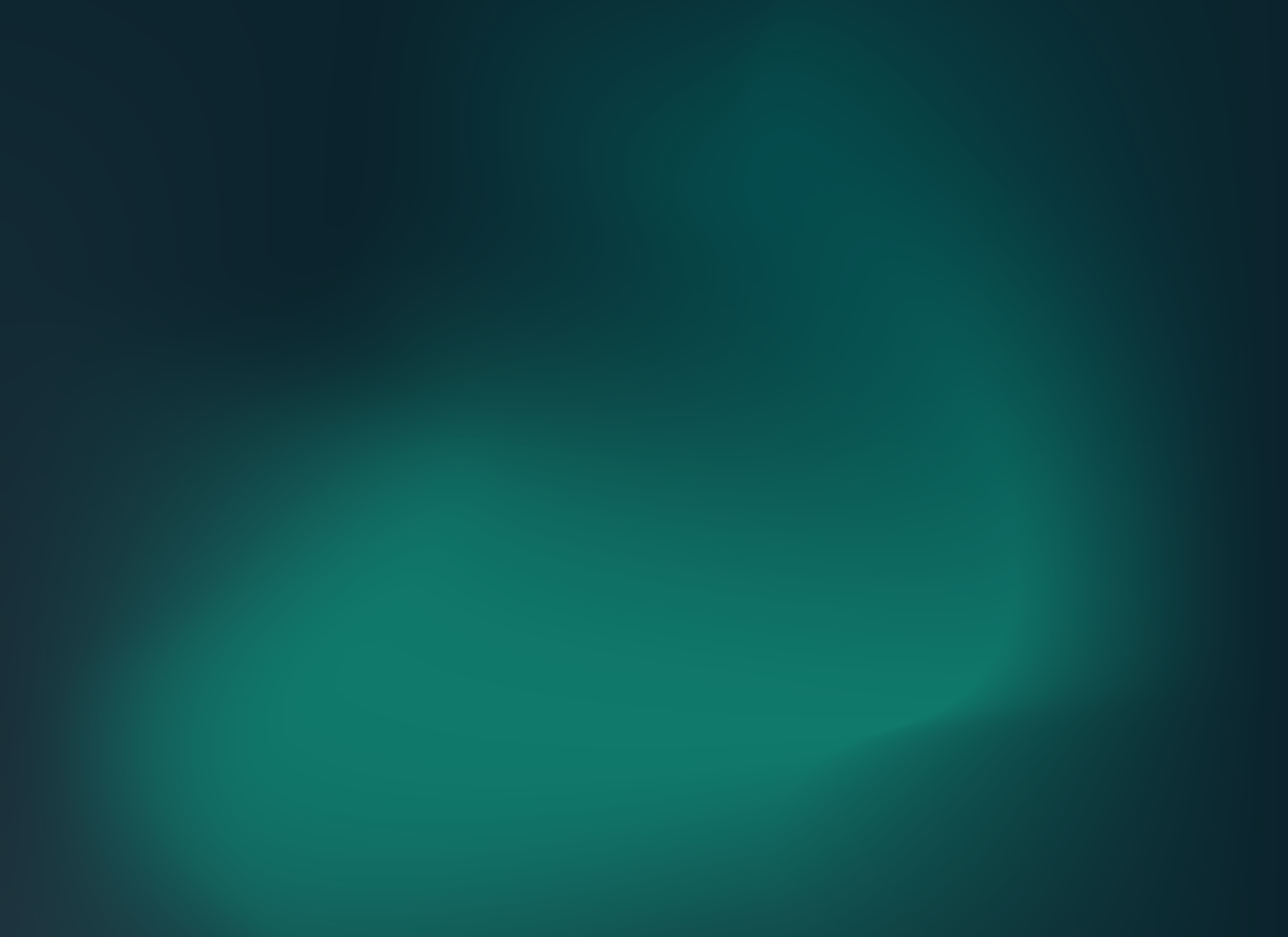
Case Study
AOGV solves onshore HSSE risk for Supermajor
An 18 inch butane pipeline, which connected a major natural gas liquids plant with its marine export terminal, had a leaking instrumentation carrier (flow meter) that needed to be isolated for replacement. With a short, three-week window to avoid both the shutdown of the entire pipeline and the need to construct a new pipeline close to the terminal, Izomax deployed its proprietary technology, facilitating an on-site solution within two weeks whilst avoiding a shutdown.
Challenges
The 18 inch class 300 butane line operating at 12 bar (175 psi) was a significant length – approximately 11 kilometers. The pipeline design made it impossible to fully drain and refill the pipeline with butane, thus utilizing conventional technologies would mean replacing the line. A variety of engineering solutions were considered which could minimize pipeline downtime whilst replacing the flow meter. Located in a residential area, the asset owner understandably wanted to avoid the risks, complex operations and major costs associated with this course of action. There were no suitable means for isolation near the maintenance point limiting intervention options for the operator. In addition, asbestos was discovered in the gasket, necessitating supplementary specialized procedures for safe handling, decontamination, replacement and disposal.
Solutions
The Izomax patented AOGV is a mechanical isolation tool which can set and retract a blind spade in a pair of flanges on a pressurised process system, without hot-work. The blind spade or a combination of several spades in different locations can facilitate the replacement of valves and pumps. The AOGV can also be used to take a vessel out of a closed loop temporarily for safe entry and bringing it back on-line, whilst the main process is kept in continuous operation.
Utilizing the AOGV mechanical isolation system enabled replacement of the flow meter by use of isolation spades on the butane pipeline, whilst minimizing gas freeing.
Testing, planning & preparation
An 18 inch ASME Class 300 AOGV was designed, engineered, and manufactured for the application. Working closely with the facility owner, we attended a HAZID and hosted a Factory Acceptance Testing at our Stavanger workshop.
Identifying Asbestos within the gasket in question, we engaged with specialist handlers in advance, whilst developing a bespoke brushing tool to safely remove any remaining debris. The performance of the AOGV was verified for high pressure services using finite element analysis and by pressure testing to 1.43 times design pressure (as per the EU Pressure Equipment Directive (PED) (2014/68/EU) and EN 13445 – Unfired Pressure Vessels prior to deployment).
Site operation
A team of five Izomax technical specialists carried out this onshore operation, lifting the AOGV into place via a mobile crane, before scaffolding and rigging was used to assemble and deploy the system. Providing positive isolation, the AOGV mechanical isolation tool inserted an isolation spade between a flange pair and a built-in isolation valve, enabling depressurisation and gas-freeing of a very short section of the pipeline. The isolation allowed for removal and replacement of the leaking flow meter, whilst keeping the -4° liquid butane inventory within the pipeline.
Outcome
Efficient completion of this project was critical. With only three weeks’ capacity in the terminal’s butane tanks, there was little time before the stream of gas from plant to export terminal would have been halted. To avoid this costly outcome, Izomax completed operations safely, within just two weeks. Several alternative solutions had been deployed to attempt to solve the external leak, without success. The Izomax AOGV mechanical isolation tool provided the only viable solution: without its ability to provide positive isolation within the pipeline, the consequences were considerably greater than a facility shutdown. Fundamentally, the AOGV mitigated the requirement to install an additional pipeline at significant cost and risk – both from an HSE and reputational perspective. The entire operation including site survey, manufacture, testing and execution at the onshore terminal was flawless with no HSE incidents or non-productive time.
As with the vast majority of Izomax AOGV mechanical isolation work, no hot work was required, saving the operator considerable time and costs related to planning and executing hot work, in addition to mitigating complex HSSE risk. The asbestos identified in the existing gasket was safely disposed of, with an approved decontamination process performed on site. System integrity was maintained throughout the operation, with plant returned to original status and condition.
The Izomax team enabled an estimated cost saving of $15m USD as a direct result of not shutting down production. This direct saving would not have been achieved without using Izomax AOGV technologies.