This website uses cookies so that we can provide you with the best user experience possible. Cookie information is stored in your browser and performs functions such as recognising you when you return to our website and helping our team to understand which sections of the website you find most interesting and useful.
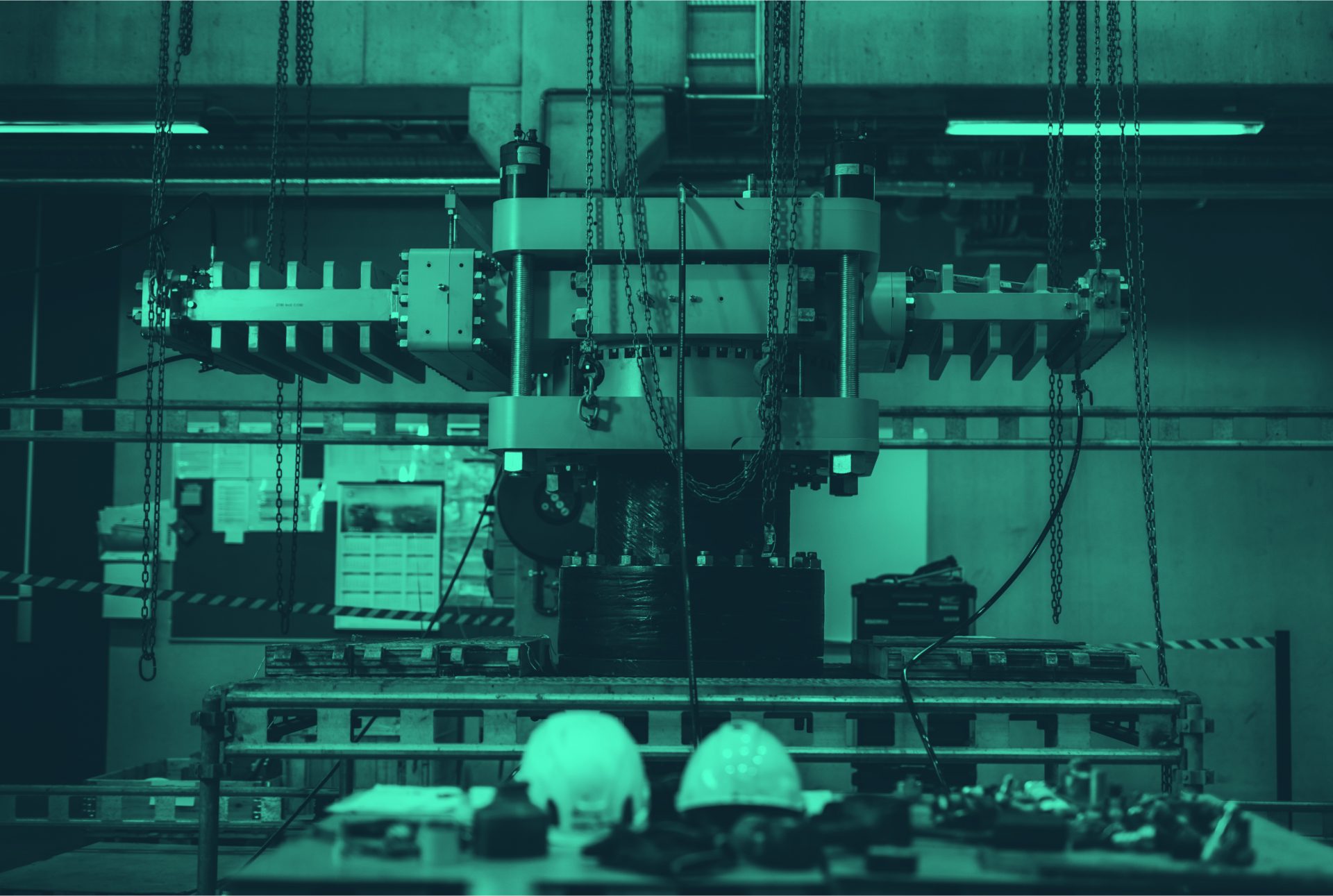
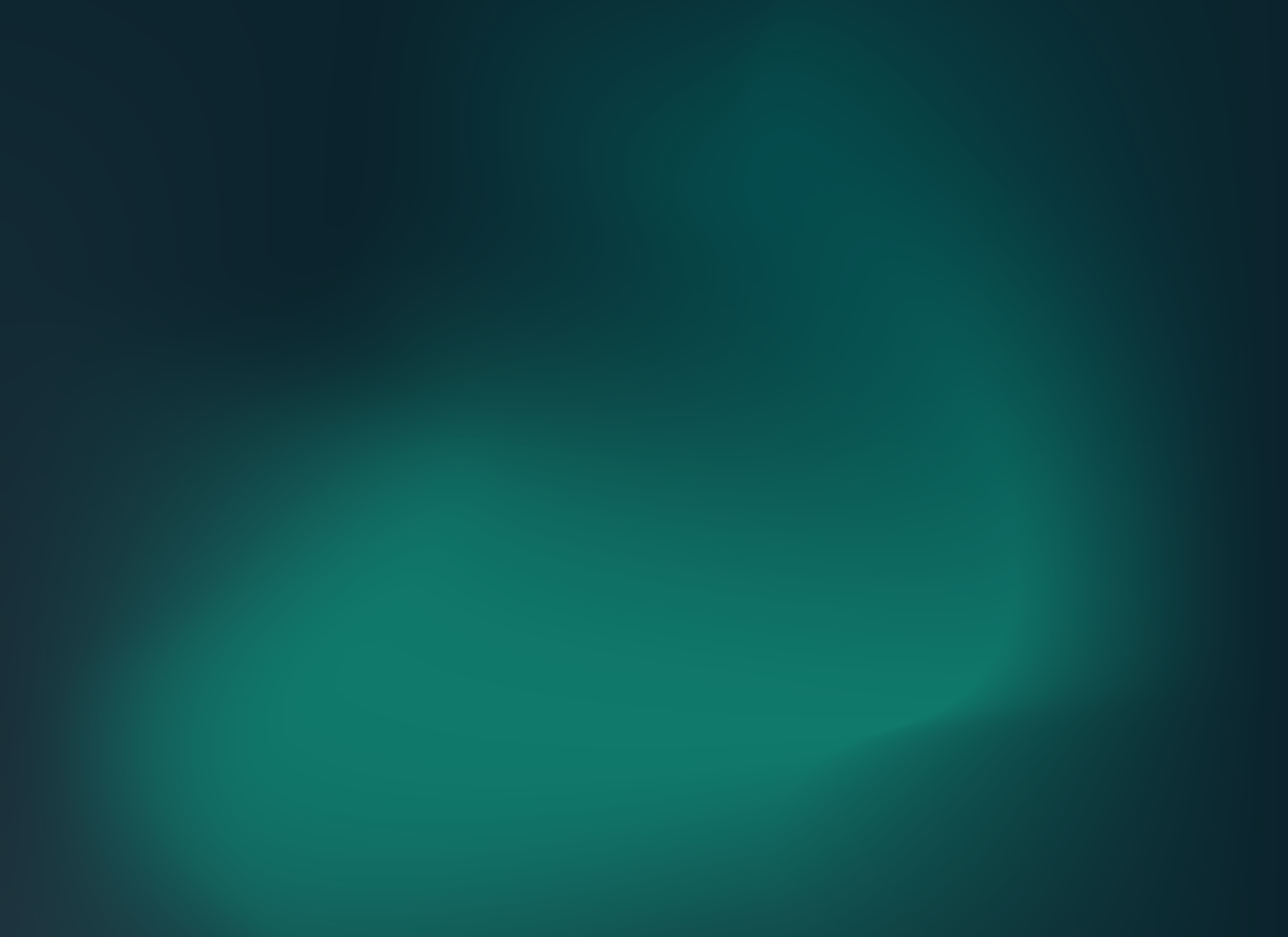
Case Study
AOGV saves time in planned maintenance stop on offshore oil & gas process plant
Regular maintenance shutdowns on oil and gas platforms and process plants are an absolute necessity but prove costly due to complexity and resulting delays in production. An FPSO operator chose to save maintenance time and increase production via deployment of the Izomax AOGV mechanical isolation technology. While built-in isolation points can require the blow down and flushing of large inventory volumes, the AOGV system can be used to bring the isolation points closer to the point of interest, as well as facilitating air gapping or positive isolation in pressurised locations.
Offshore pressure vessels need regular maintenance, which is frequently performed during shutdowns, as most are critical to plant production. In this case, three vessels on the FPSO needed attention; two first-stage separators as well as the flare knock out drum.
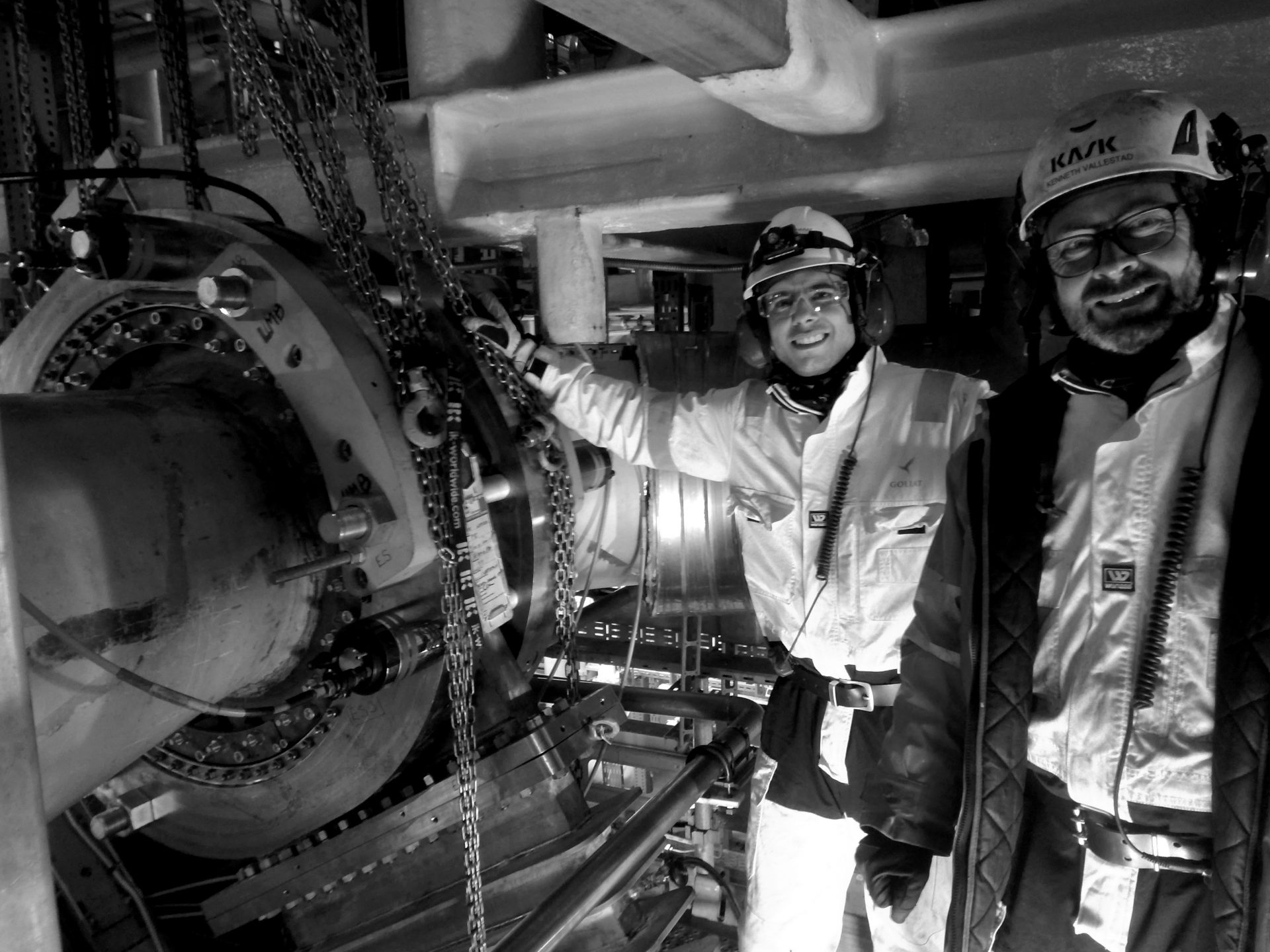
Challenges
To optimise the performance of inlet separators, the FPSO required internal parts replacement. Taking place during a scheduled maintenance shutdown, component replacement required personnel to enter the confined space of the separators, thus requiring emptying, cleaning, and degassing. The existing plant had no valves or means to isolate the separators. Hot work carries additional risks, cost, and complexity offshore, and can be avoided using Izomax mechanical isolation systems. Isolation was critical due to the presence of hydrocarbons in the system. In this instance, the isolation needed to be performed on large 24 inch flanges. The required isolation of the separators from the rest of the system, including the riser, was not possible. The commonly used solutions utilise the flare system to bleed off all relevant systems after which the flare system can be gas freed. To ensure the entire system is free of gas using standard solutions, the shutdown period required for preparation time alone would be extended by between three and five days. The Izomax team focused on processes and technologies to avoid or mitigate such lengthy periods of time.
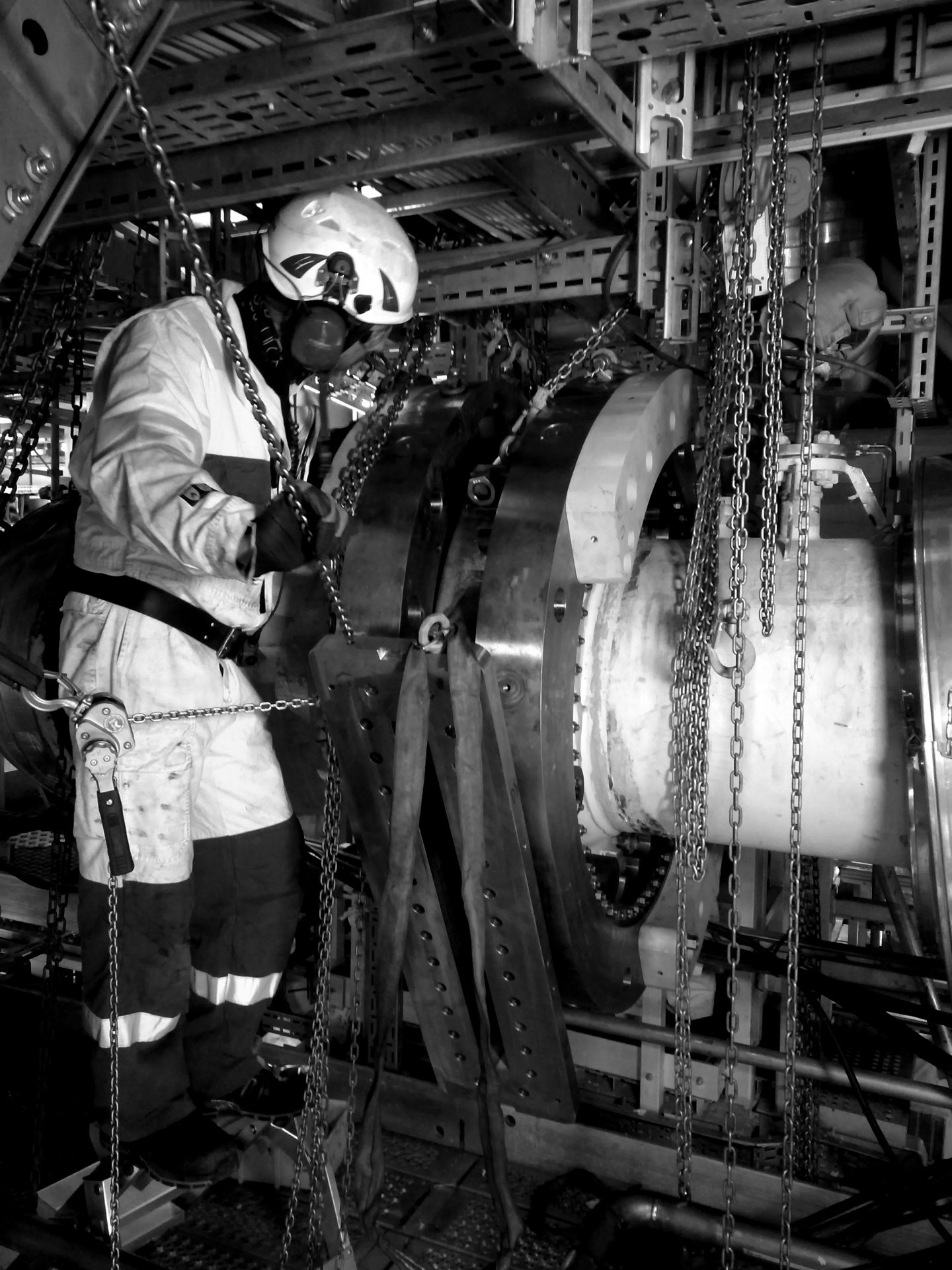
Testing, Planning and Preparing
The AOGV mechanical isolation system was selected early in the planning phase to reduce the shutdown length to a minimum. For the separator work, a short timeframe meant that two AOGV mechanical isolation tools of the same size were deployed – one on each of the parallel systems. Izomax performed an on-site survey with measurements and 3D scanning, ensuring a perfect fit between the AOGVs and flanges. The two 24 inch locations had previously been successfully used for AOGV operations, whereas obstacles on the 4 inch flange required the AOGV integrity clamp to be redesigned for a perfect fit.
Solutions
Working towards a common timesaving objective, an additional work scope took place concurrently, allowing for efficient maintenance of the knock out drum. By providing positive isolation for the knockout drum from the rest of the flare system, the Izomax AOGV mechanical isolation tool cut the length of shutdown by approximately two additional days as a direct result of reducing the level of preparation work required.
The AOGV – mechanical isolation tool
The Izomax patented AOGV is a mechanical isolation tool which can be temporarily assembled on any pair of flanges in a pressurised process system. The tool is used to replace gaskets, install, and retrieve blind spades to facilitate intrusive maintenance. The blind spade or a combination of several spades in different locations can replace the function of valves and provide positive isolation for vessels, valves, or parts of a process plant. Bleeding or purging through the blind spade can also be facilitated. The AOGV design meets the requirements as per EU Pressure Equipment Directive (PED) (2014/68/ EU) and EN 13445 – Unfired Pressure Vessels.
Testing, planning and preparation
The AOGV mechanical isolation system was selected early in the planning phase to reduce the shutdown length to a minimum. For the separator work, a short timeframe meant that two AOGV mechanical isolation tools of the same size were deployed – one on each of the parallel systems. Izomax performed an on-site survey with measurements and 3D scanning, ensuring a perfect fit between the AOGVs and flanges. The two 24 inch locations had previously been successfully used for AOGV operations, whereas obstacles on the 4 inch flange required the AOGV integrity clamp to be redesigned for a perfect fit.
Site Operation
To isolate the separators the two 24 inch AOGV mechanical isolation tools were mounted, and pressure tested on the actual flanges before plant shutdown. When production stopped, isolation spades were set to isolate out the required area. The AOGV mechanical isolation tools remained mounted on the flanges throughout the shutdown, enabling a fast retrieval of the isolation spades as soon as the maintenance stop was completed. Both flange pairs received new seals and flange bolts prior to rigging down the AOGV mechanical isolation tools, and the FPSO was already back in production whilst the AOGV tools were dismantled. Once all systems were gas freed, the flare system was ready for maintenance. The 4 inch 300# AOGV mechanical isolation tool was installed, and a spectacle blind was removed prior to installation of a blind spade on the flare line, allowing safe entry and inspection of the knockout drum. After the inspection, the spade was removed, and a spacer ring with gaskets were installed, using the AOGV system. Once the flange pair was restored to its original state the flare system was ready for the FPSO to resume production.
Outcome
The entire operation including site survey, manufacture, testing and offshore work was performed on-schedule by Izomax personnel, without HSE incidents or non-productive time. As with the vast majority of Izomax AOGV mechanical isolation work, no hot work was required, saving the operator considerable time and costs related to planning and executing hot work, in addition to mitigating complex HSSE risk. System integrity was maintained throughout the operation, with plant returned to original status and condition. The FPSO maintenance program involved more than 200 people, giving extra significance to the 2 days by which Izomax technologies reduced the maintenance period. In addition, the Izomax AOGV mechanical isolation tool saved the customer between 5 – 7 days of delayed production when compared to traditional technologies.
